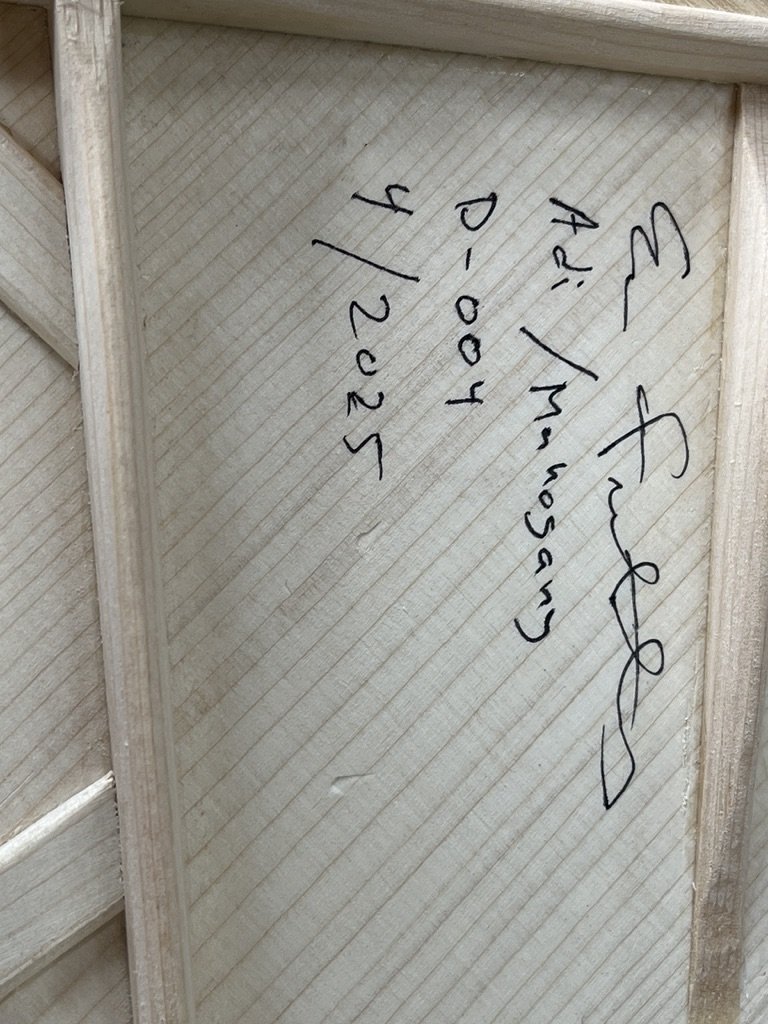
This is not my guitar, but I made it!
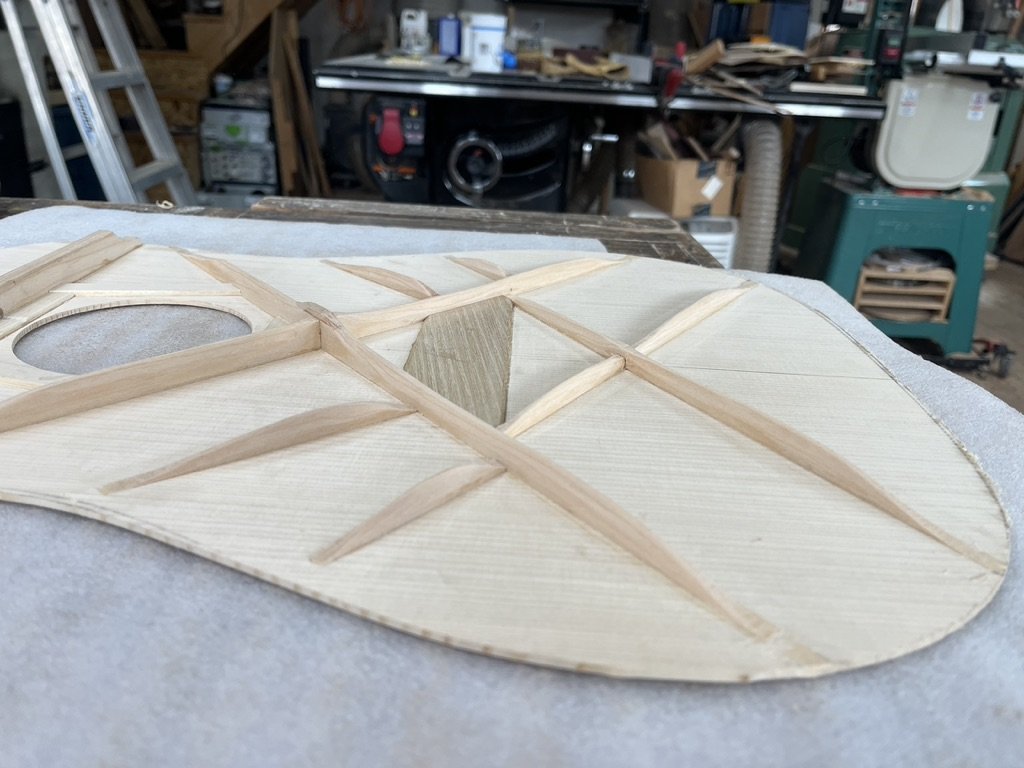
I’ve been working on hybrid scalloped/tapered bracing, to provide fast attack and lots of overtones.
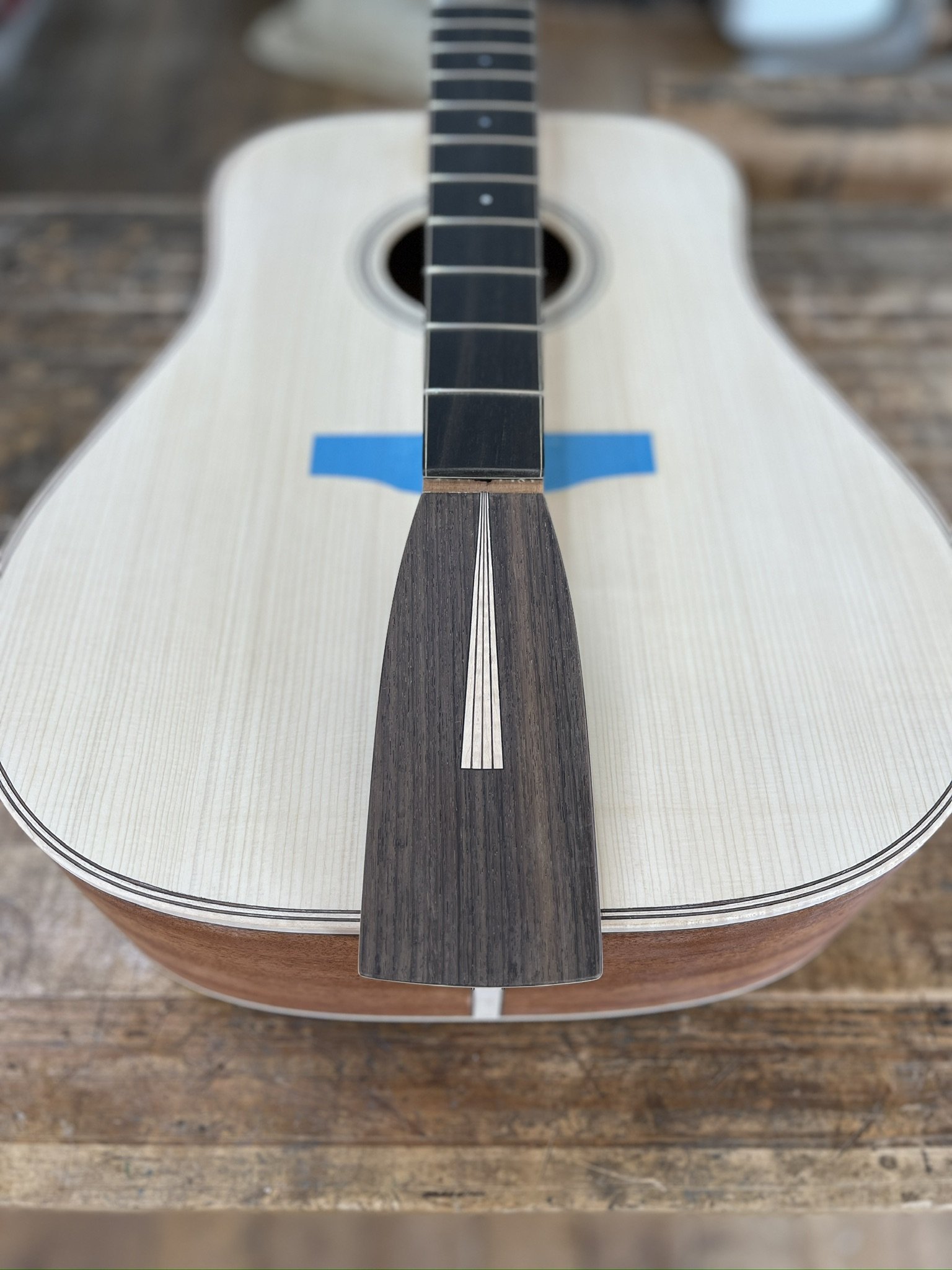
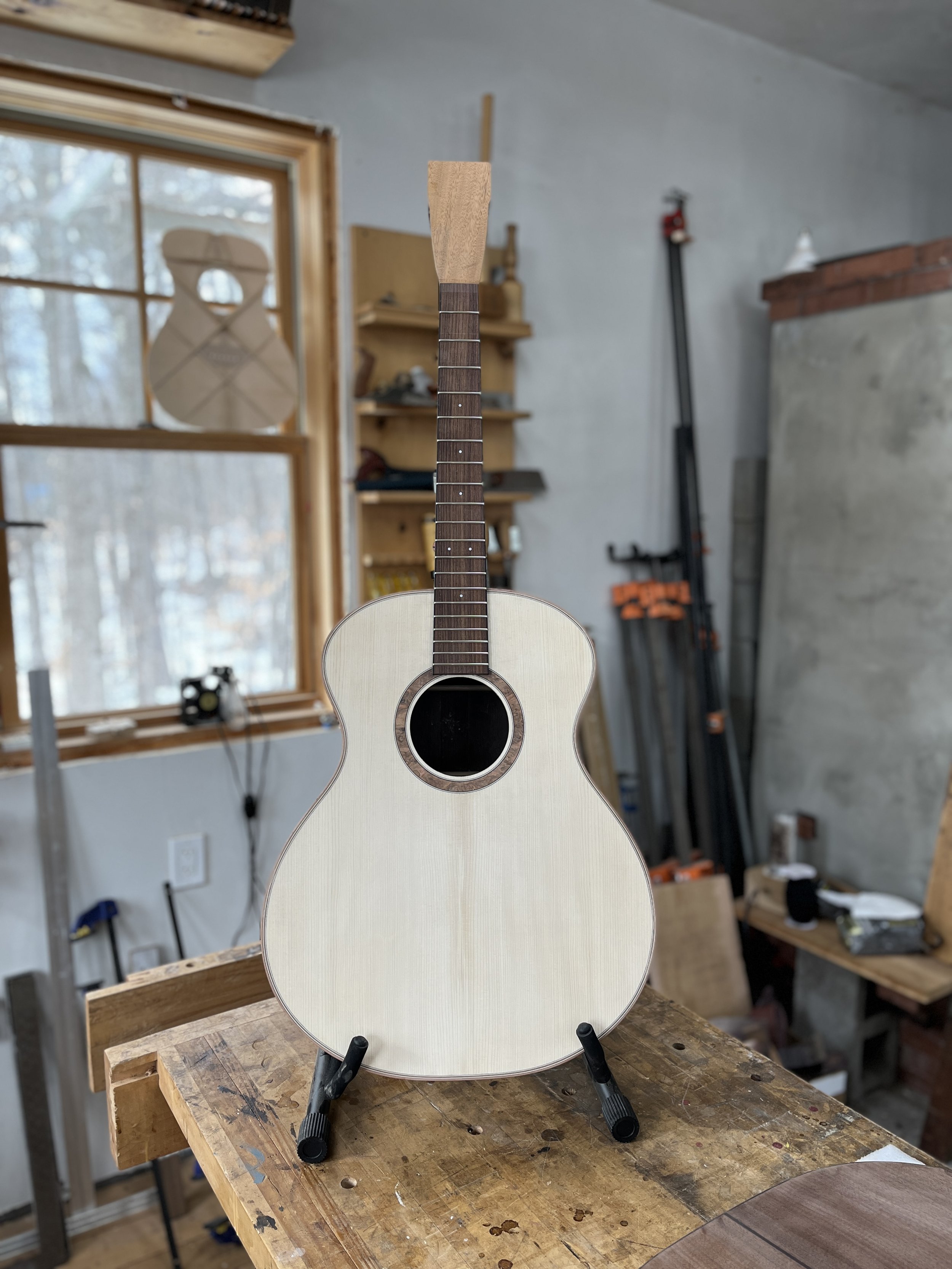
Red spruce, rosewood fingerboard with ebony binding.
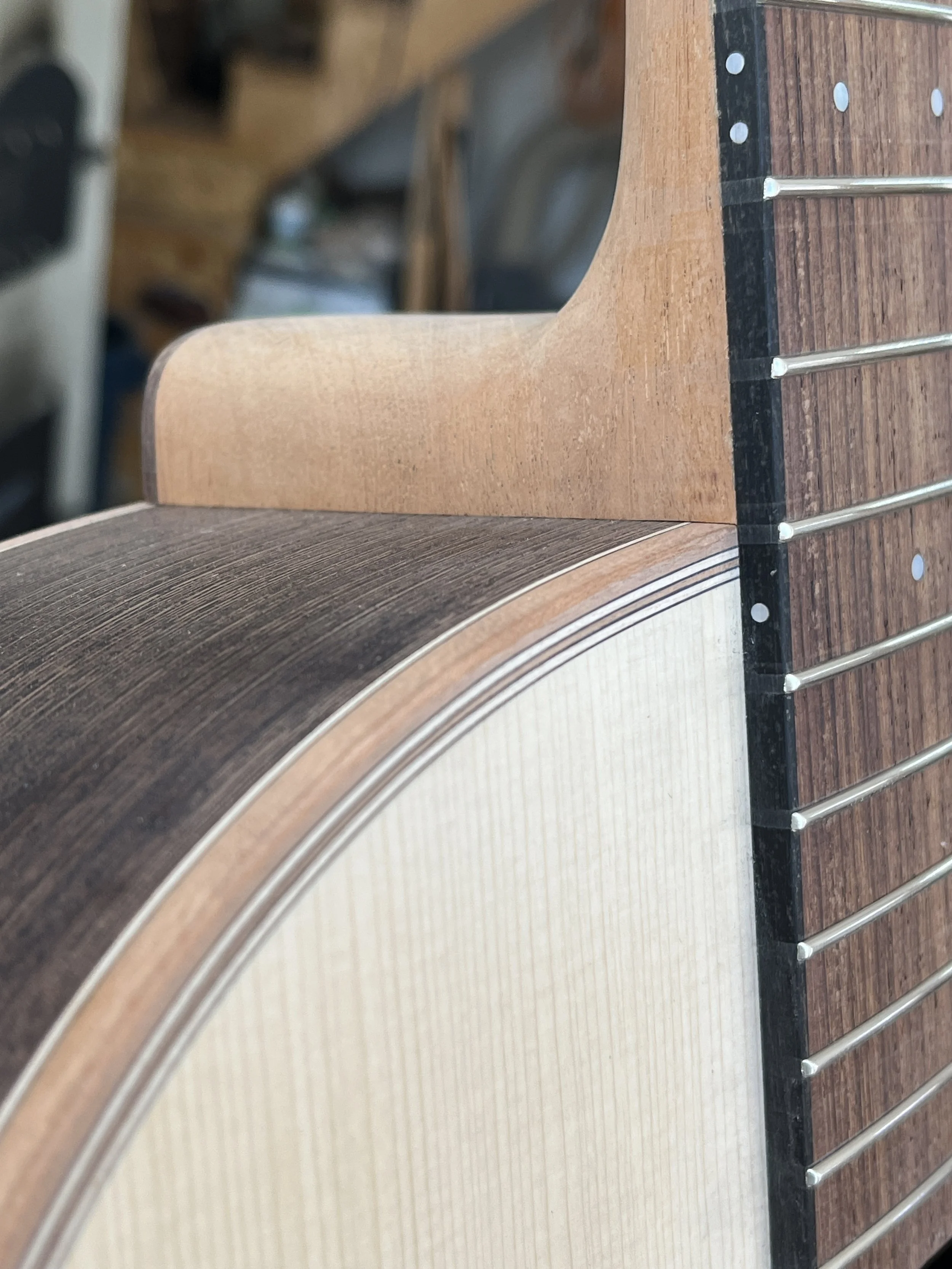
Cherry binding with black/maple/jatoba purfling.

Wenge back and sides, mahogany neck
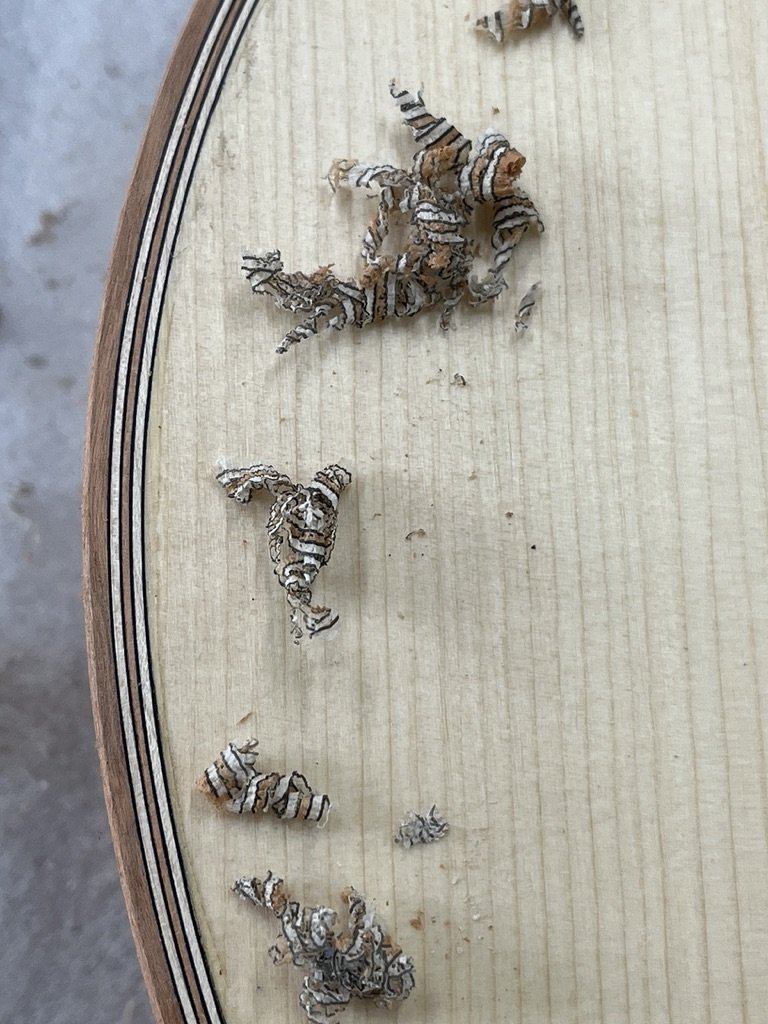
I love the striped shavings from a handplane
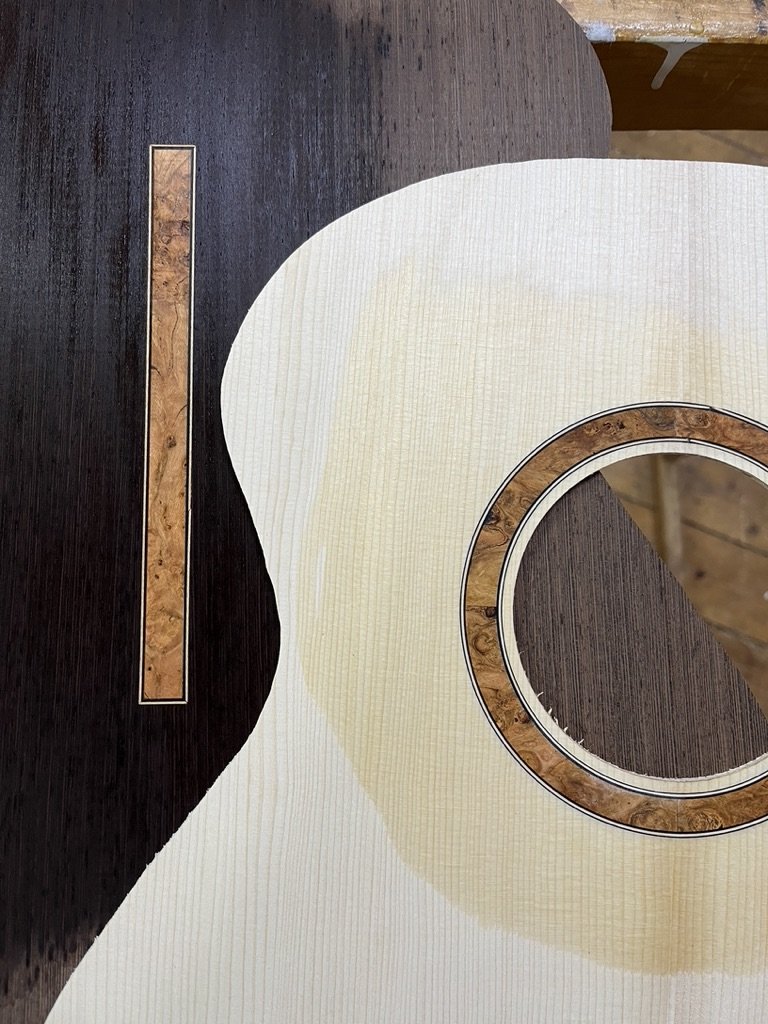
Detail of Cherry burl rosette and back inlay
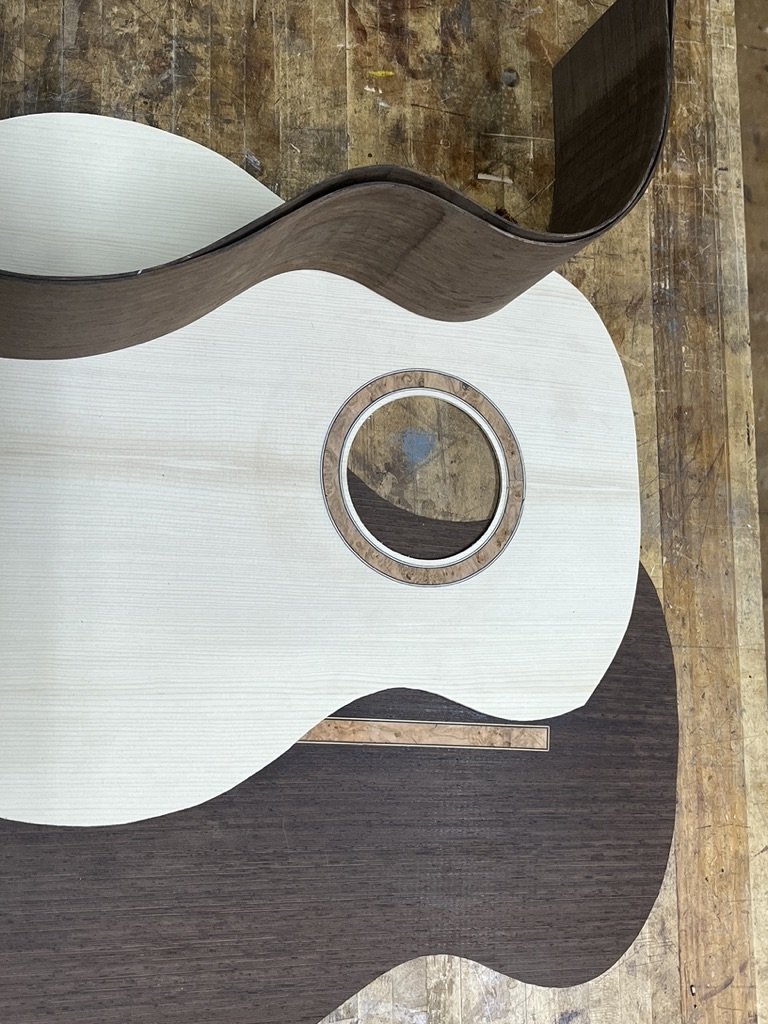
Beginnings of a Small Jumbo for fingerstyle players.
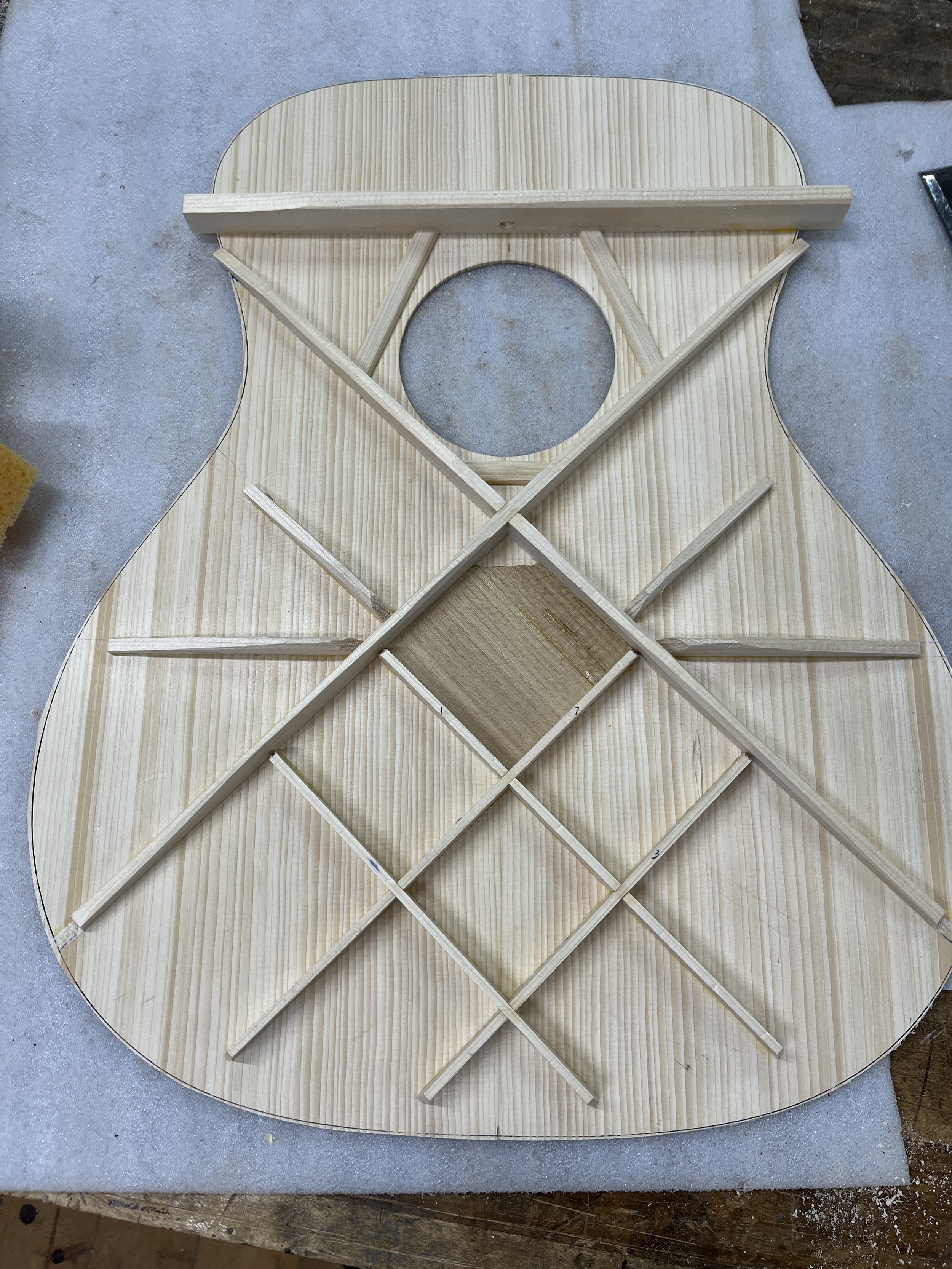
Never stop learning. This is a X-lattice hybrid bracing developed by Ervin Somogyi and used by many modern builders. It gives the builder much more control over voicing the instrument.
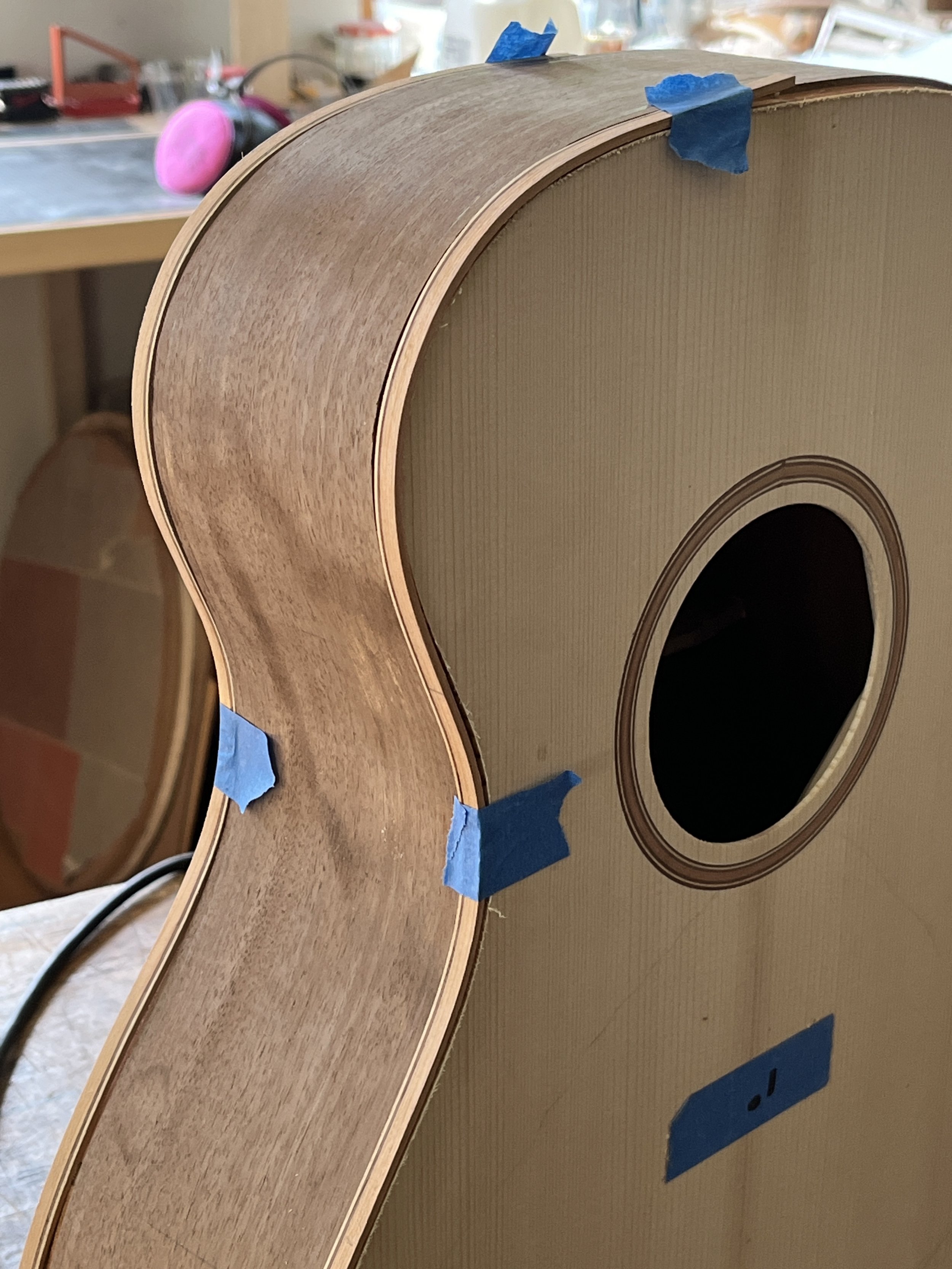
Almost there…these need to fit perfectly. It is a time consuming process.
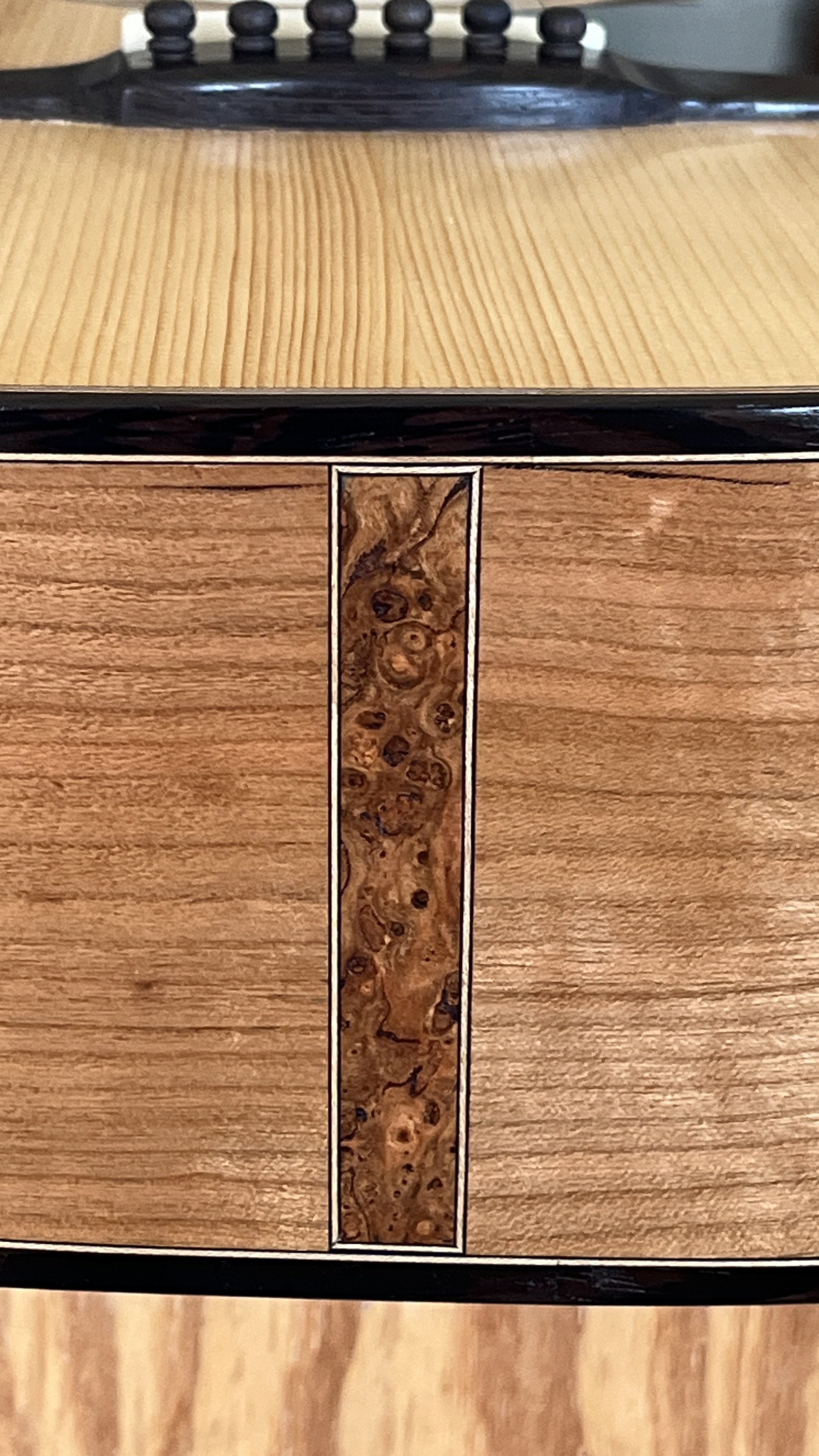
End graft using local cherry burl
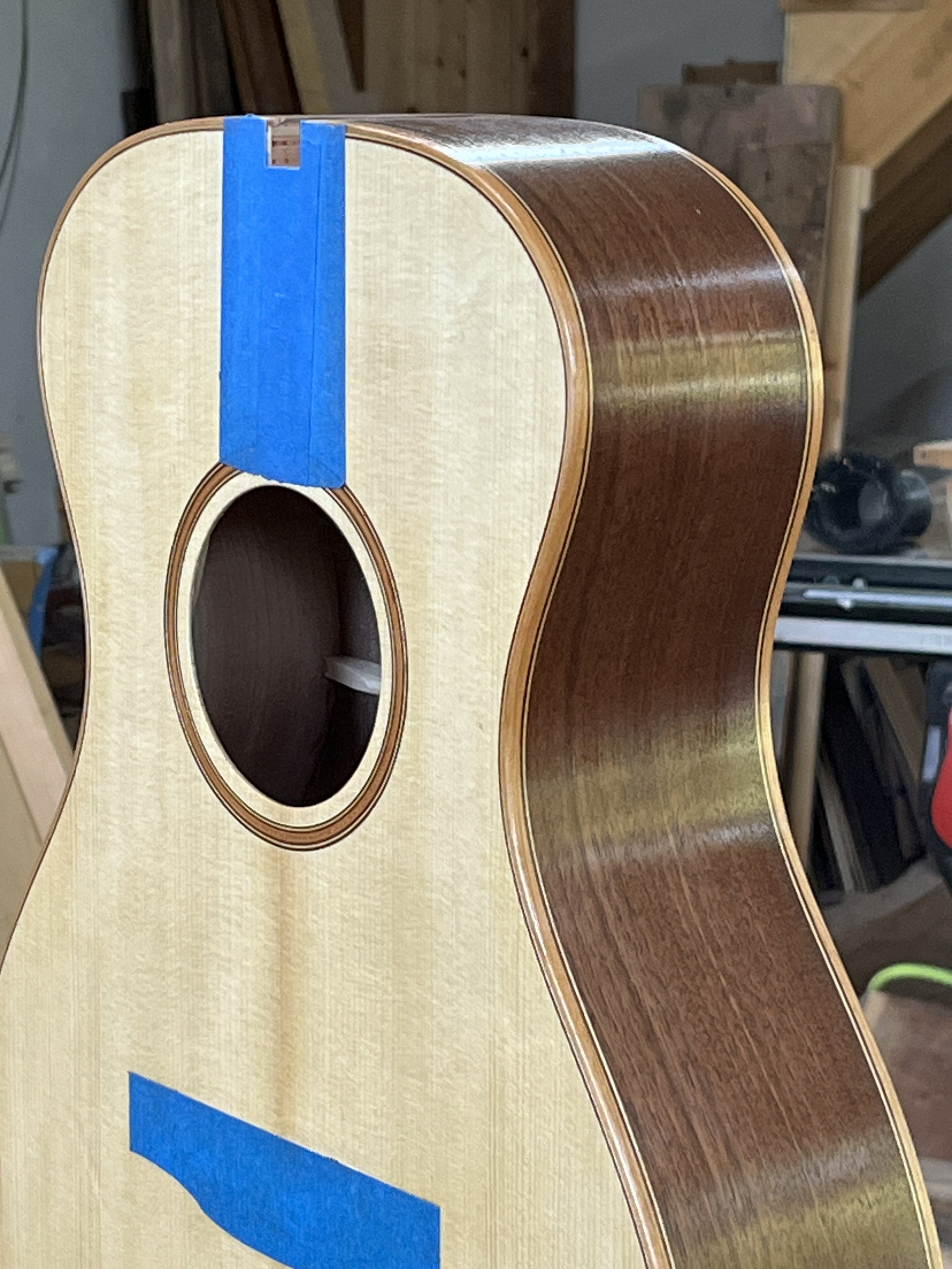
I love finishing guitars…after all the time and effort, it is so great to see them with finish.
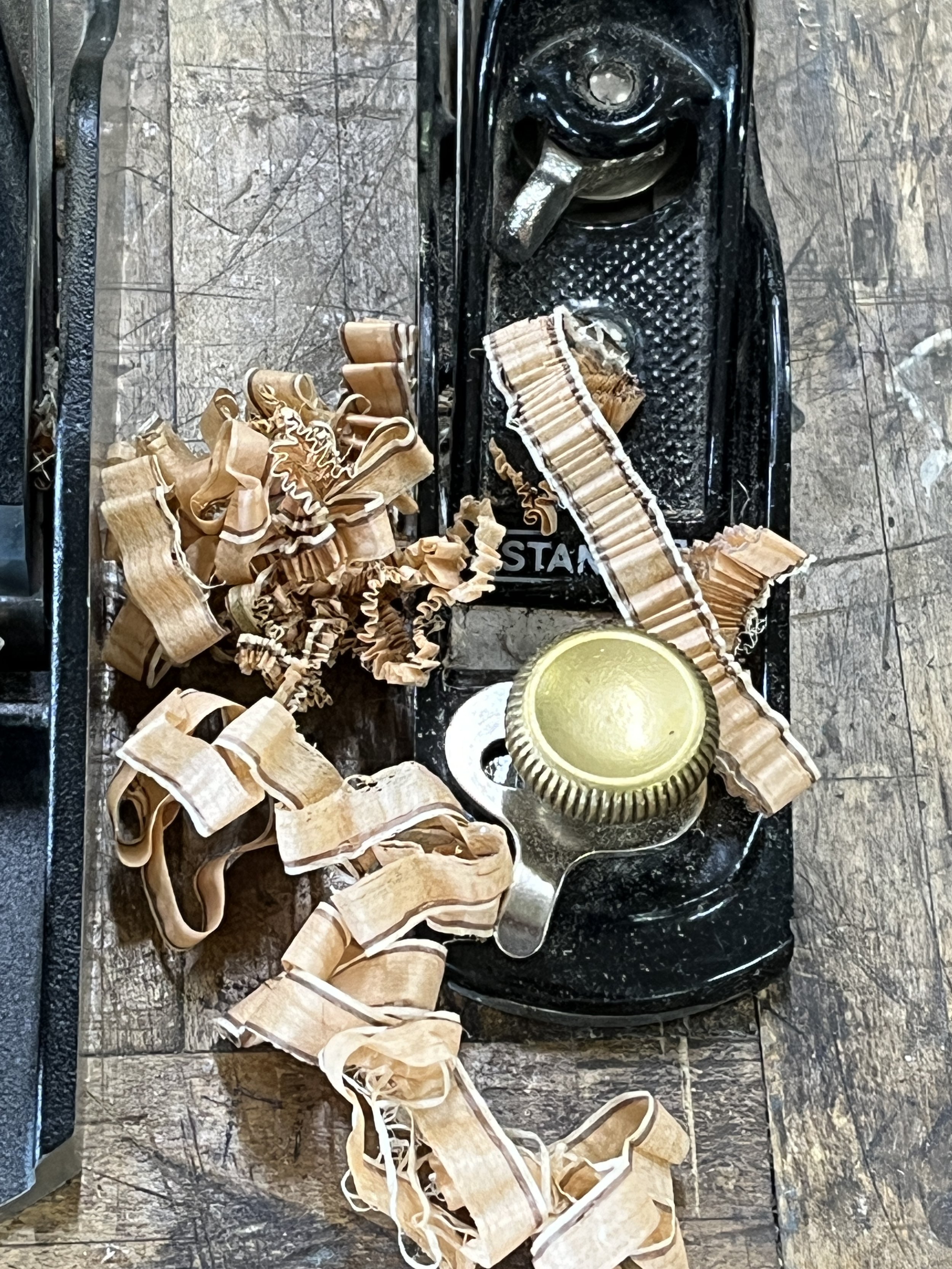
Nothing beats a handplane for fine work.
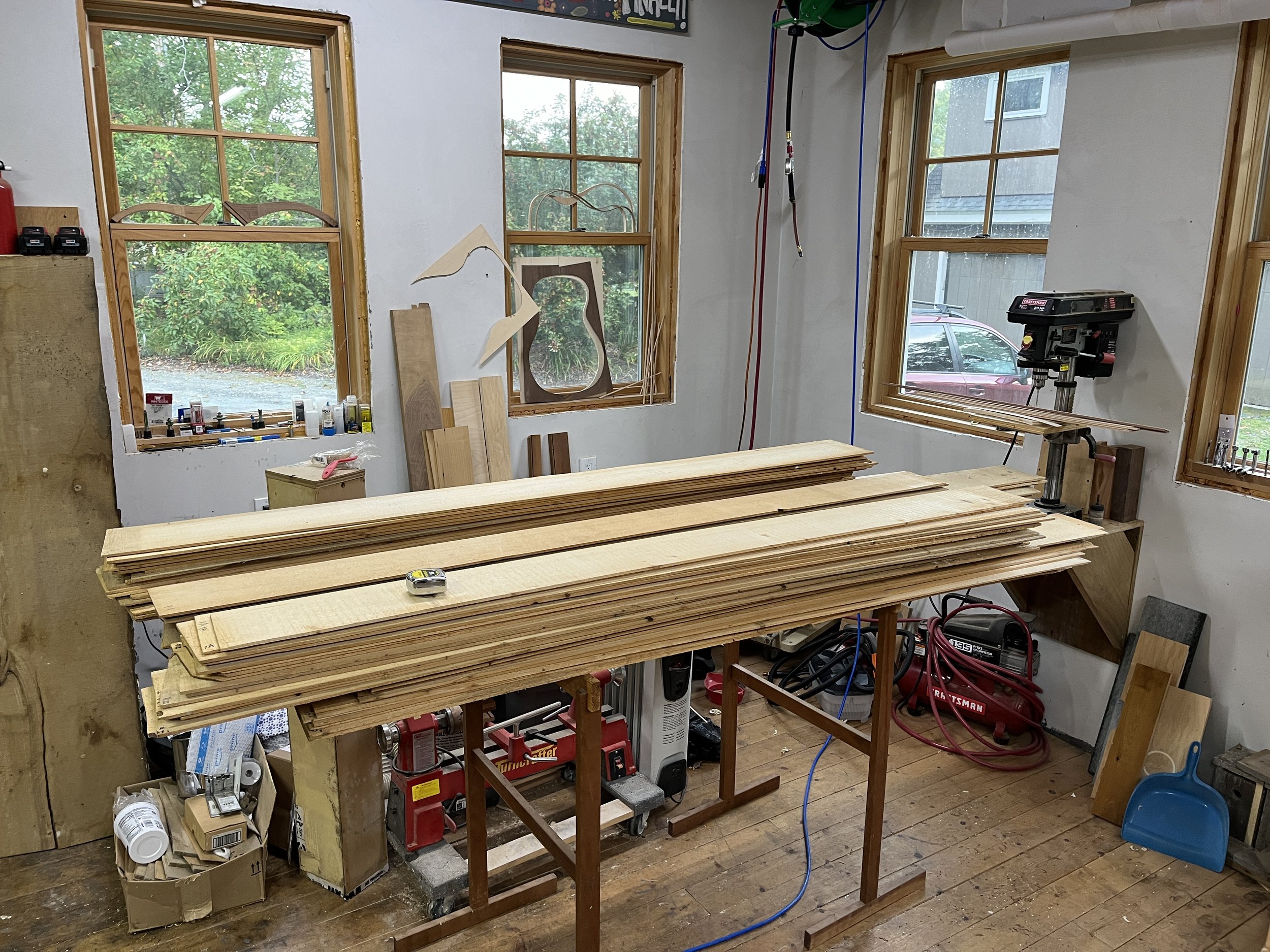
A load of red spruce ready for processing/grading. Grown in Lyme NH. I am so lucky to be able to work with this excellent material!
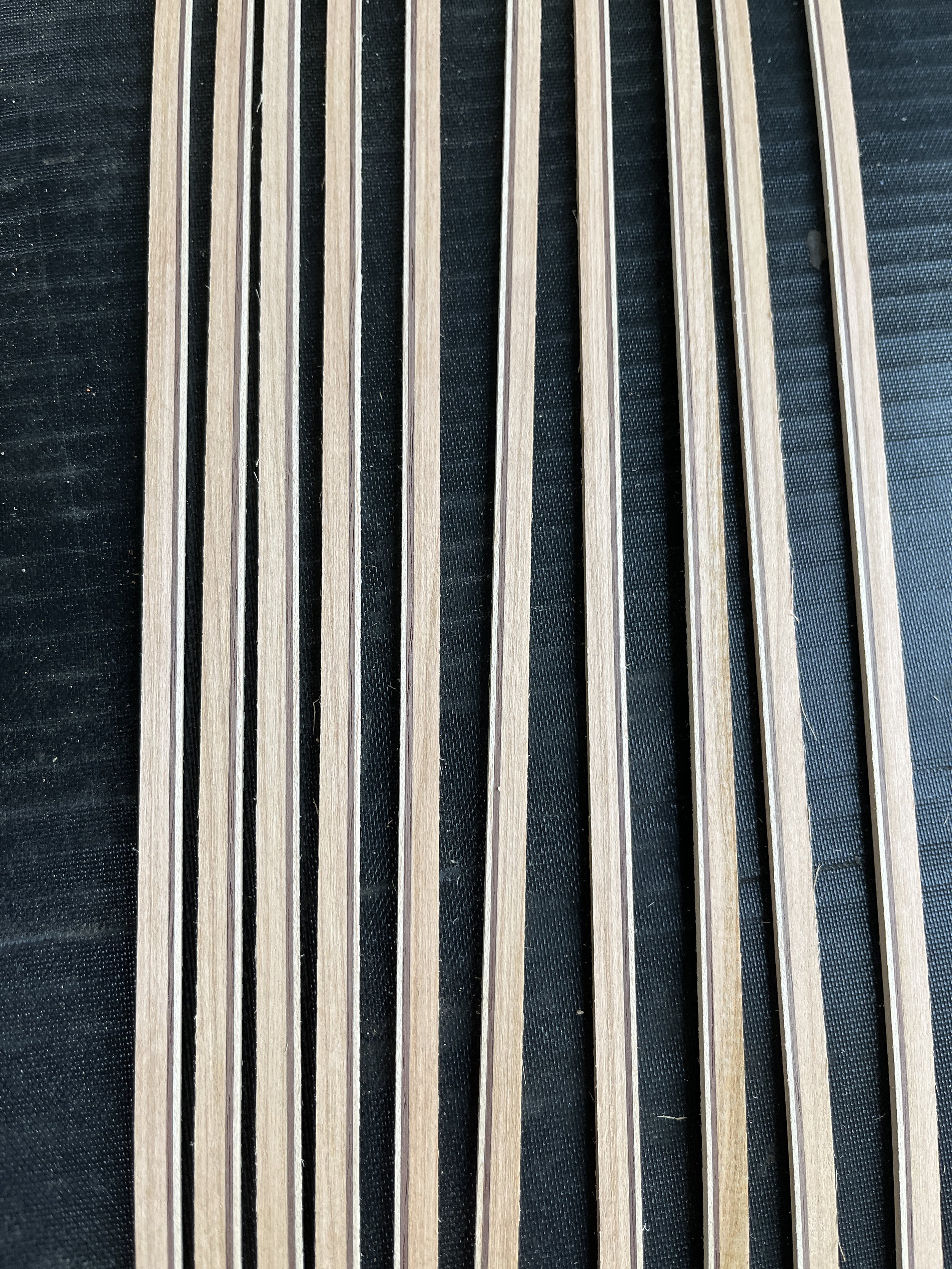
Binding and side purfling ready for bending and fitting. I see a few extras…there is always some breakage.

Modern headstock/neck volute. Provides extra support for the headstock/neck and a nice backstop for your hand.
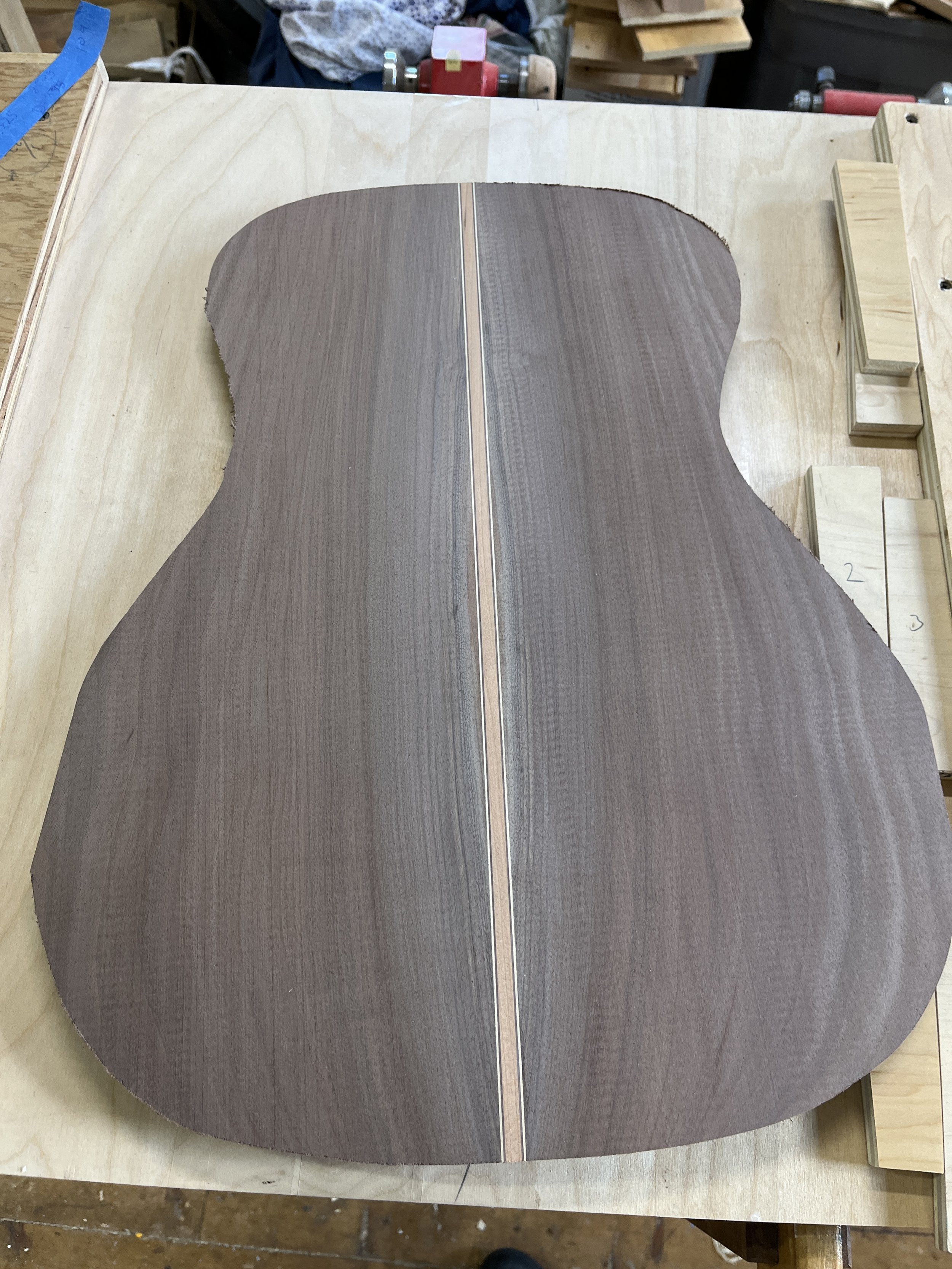
Local walnut back after trimming.
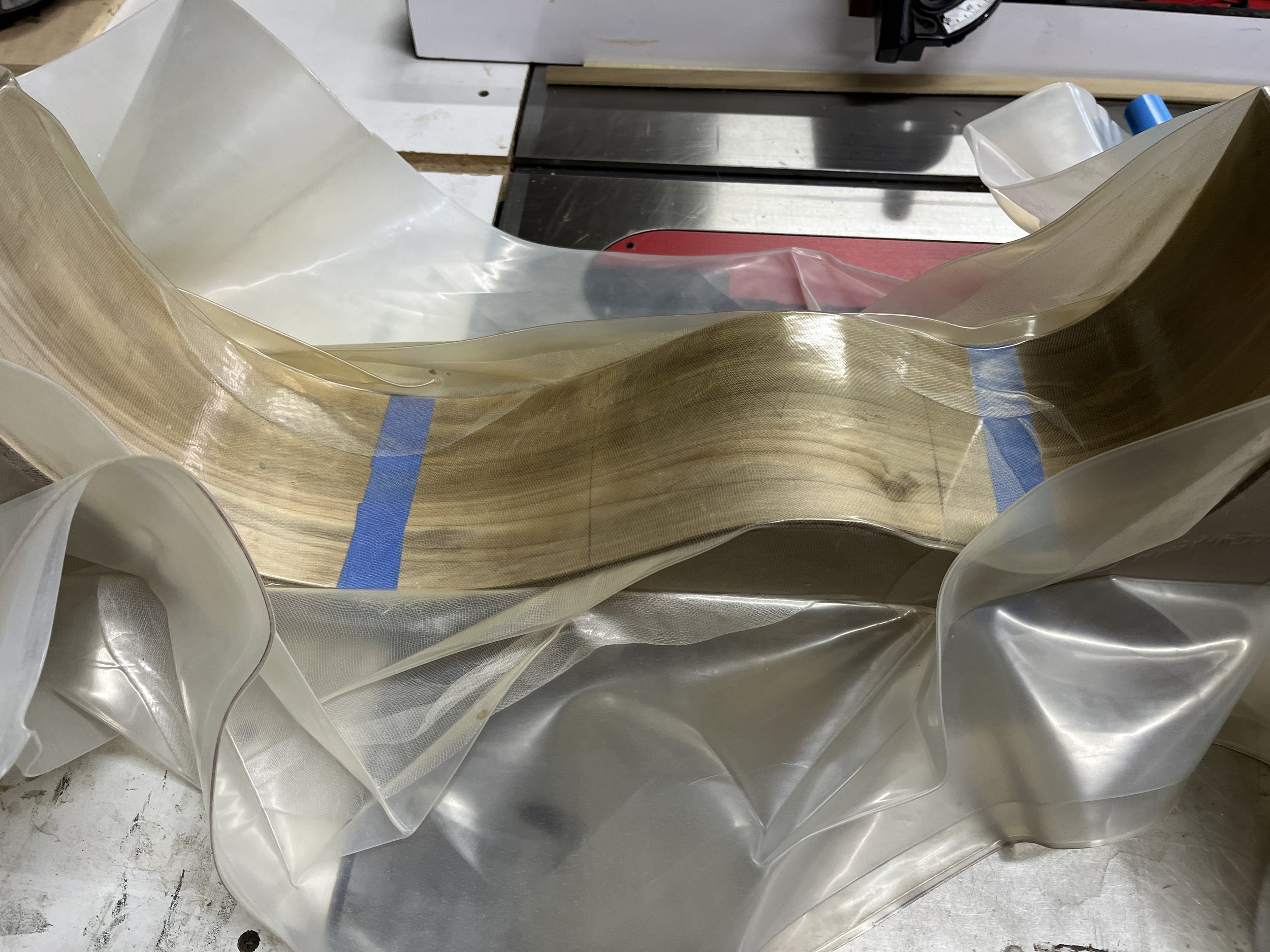
Side laminations resting in the vacuum bag before gluing.

Amazing!

Local spalted elm soundhole rosette and wenge and maple binding/purfling.

Harvested locally
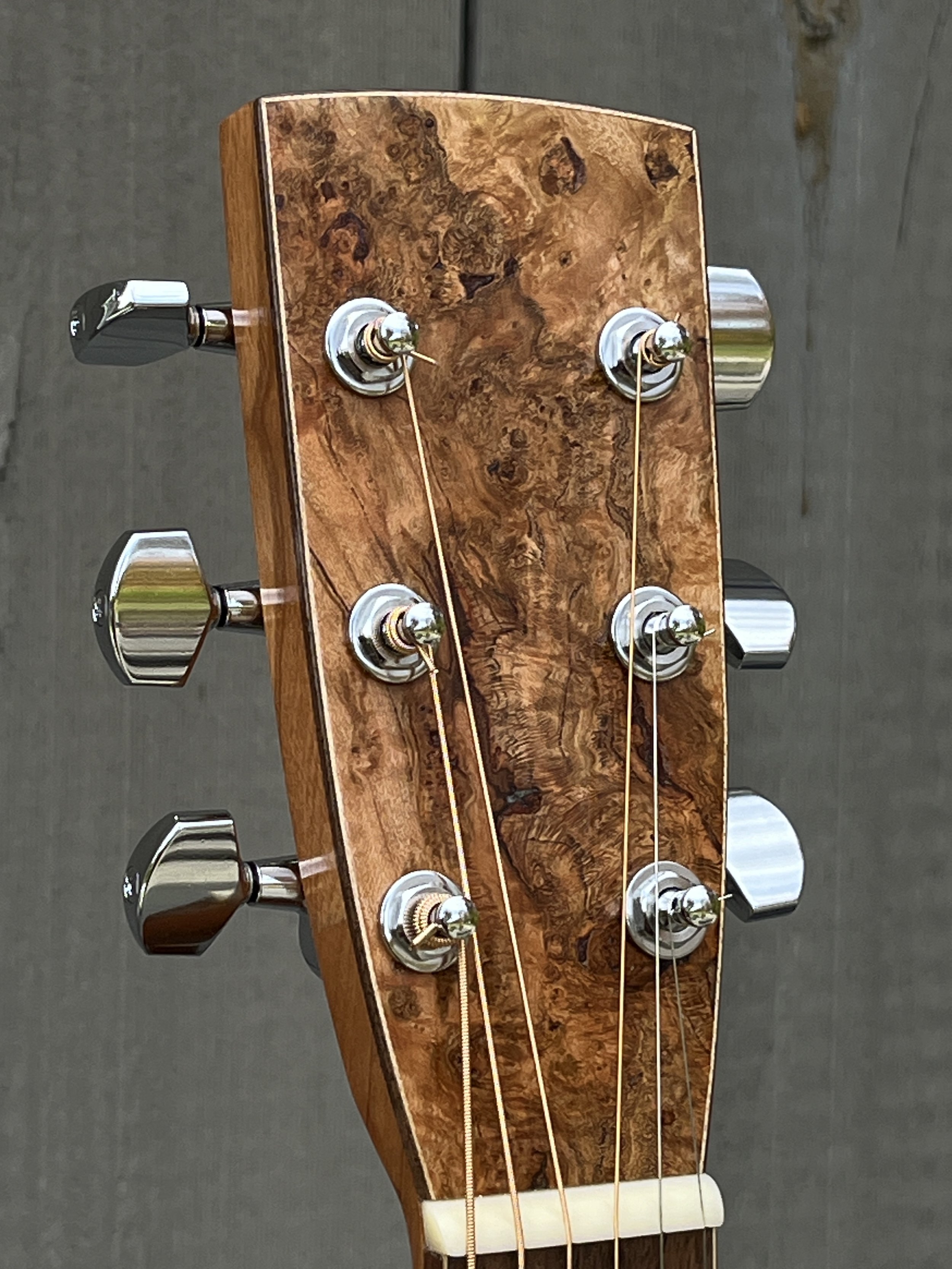
Harvested locally
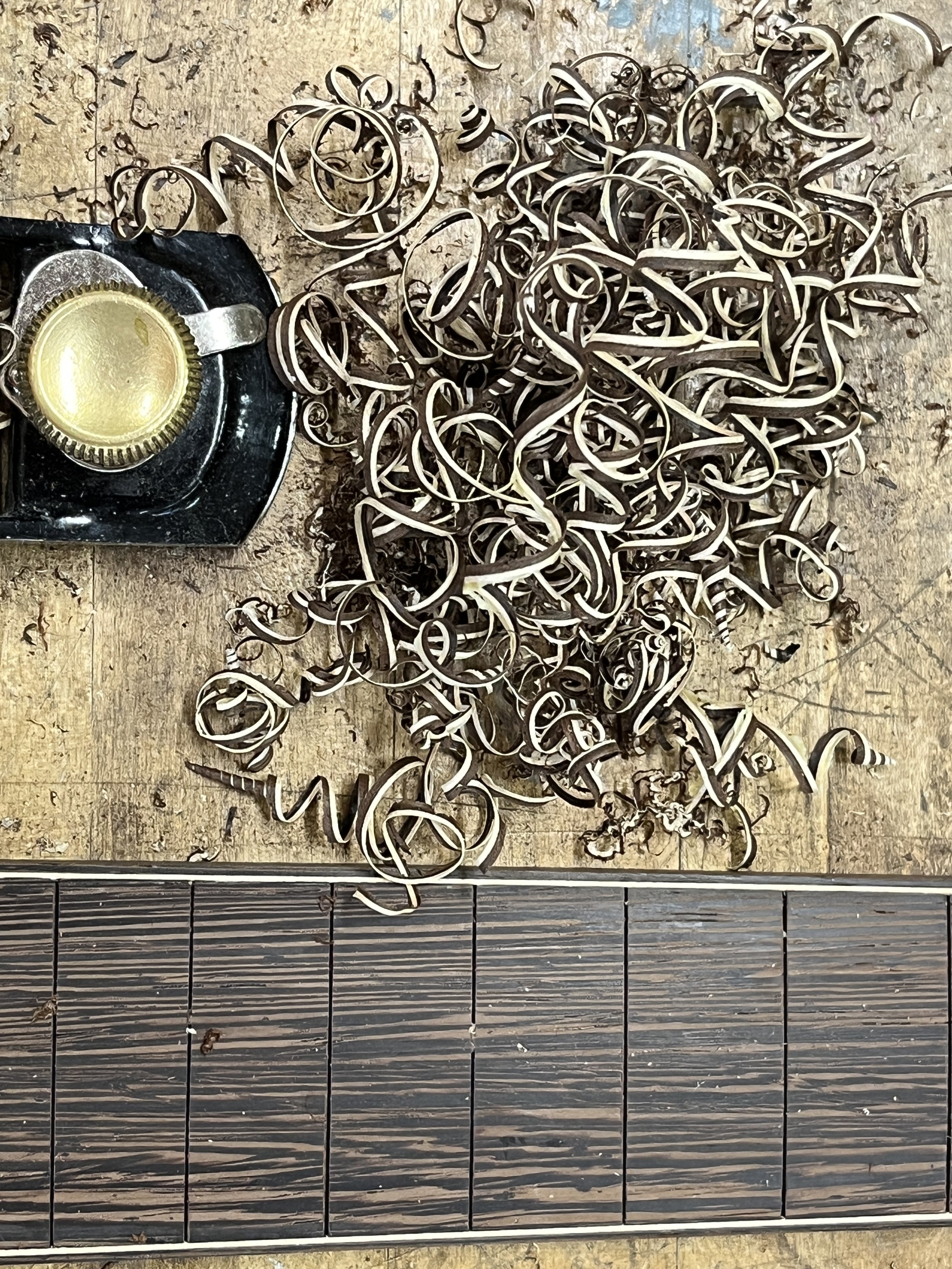
Trimming fingerboard binding. Sneak up on the perfect fit.
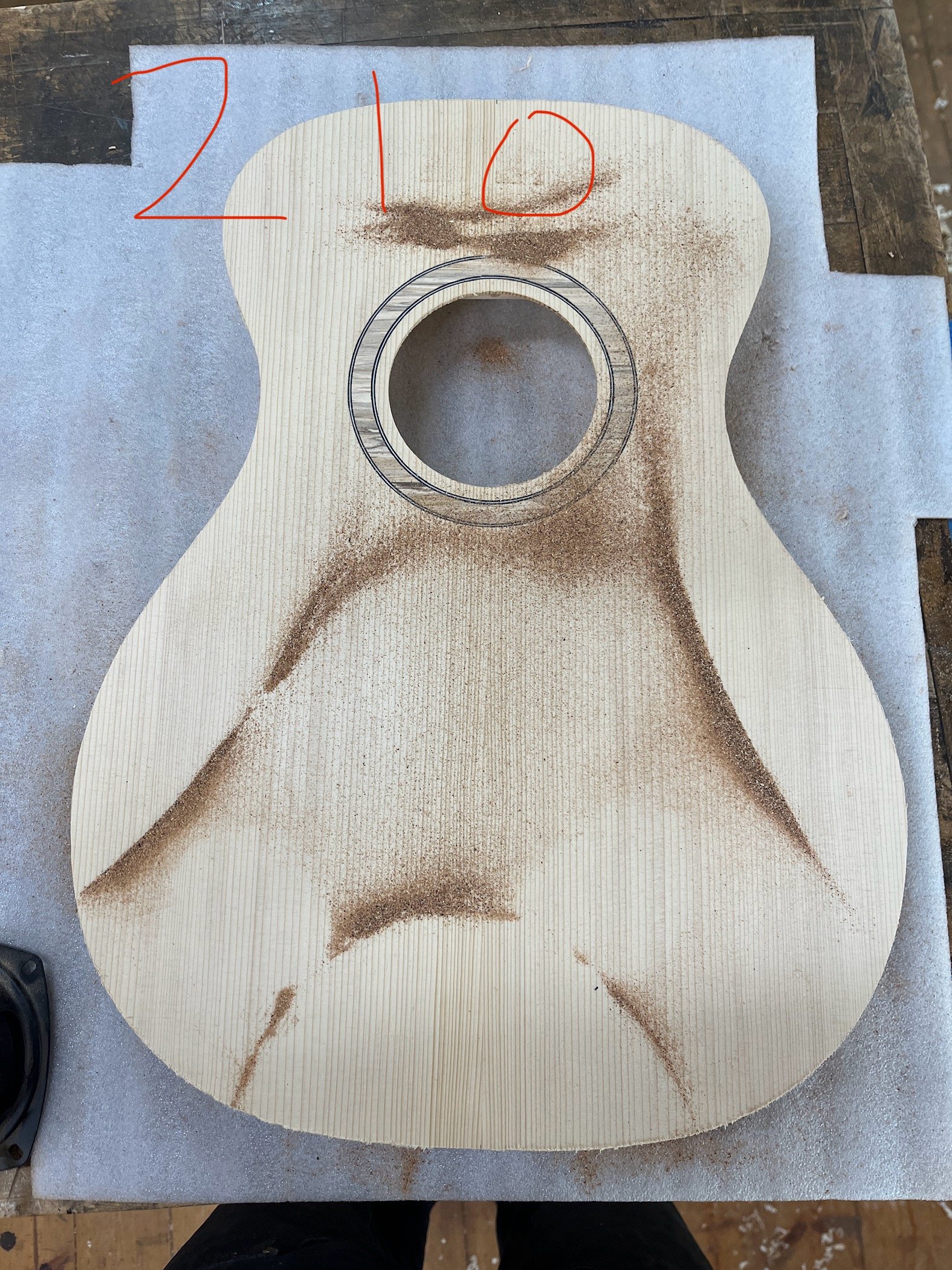
Using Chladni patterns to tune a soundboard. This involves driving a top at different frequencies to identify different modes of vibration
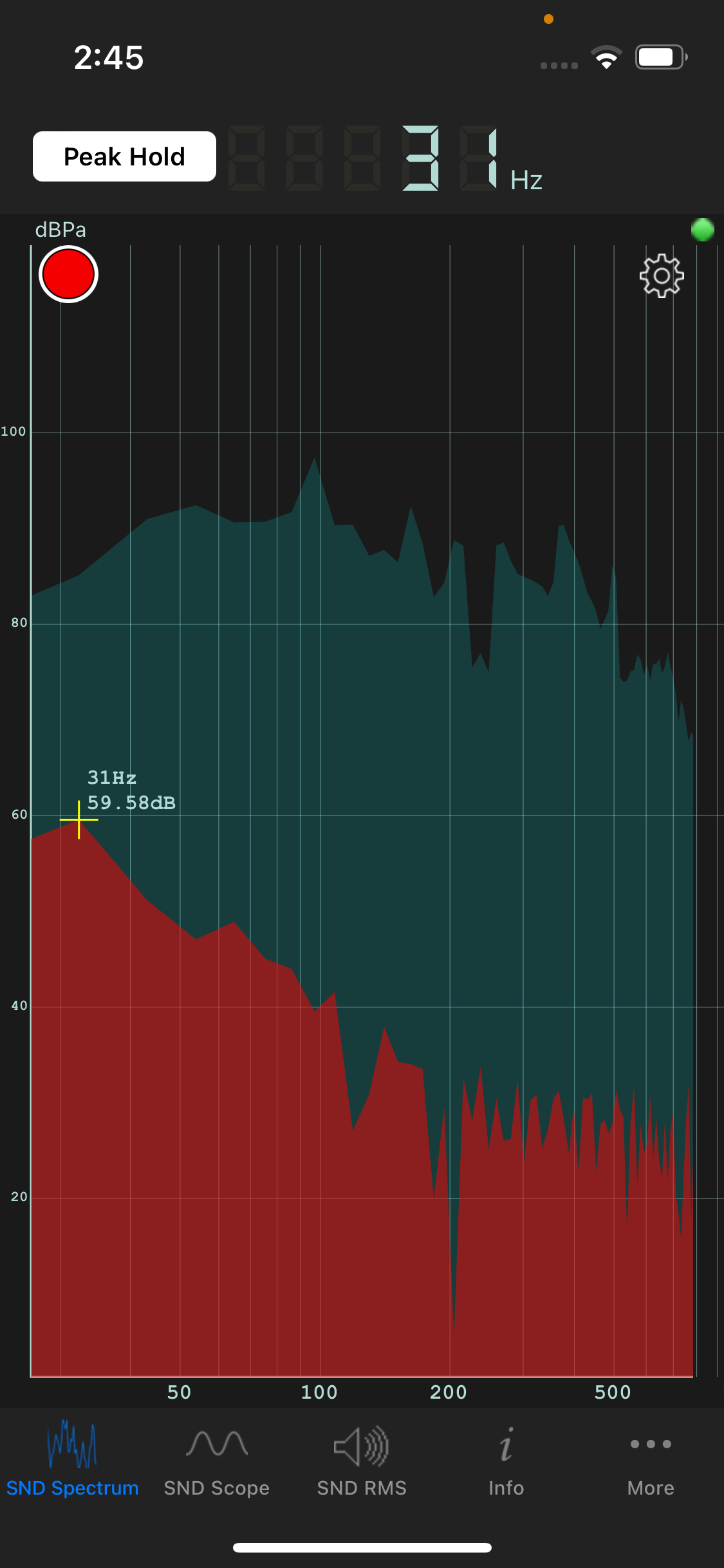
Using the frequency spectrum to tune a top.

Local black locust logs awaiting processing into billets for backs and sides. Black locust is an excellent alternative to imported rosewood.
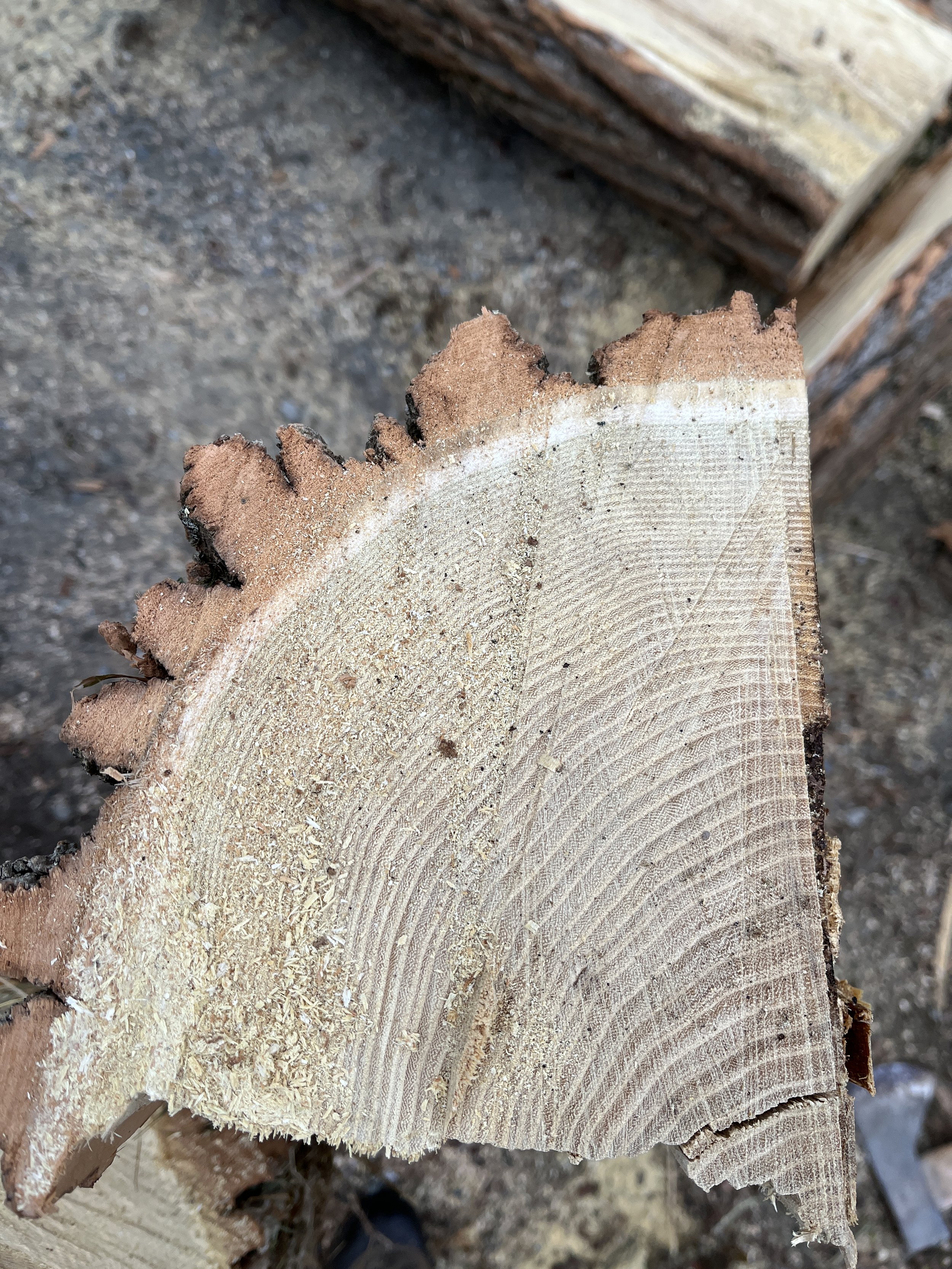
Black locust split and quartered by hand. This yields straight billets with perfect vertical grain. For the guitar this means stronger and more resonant backs and sides.
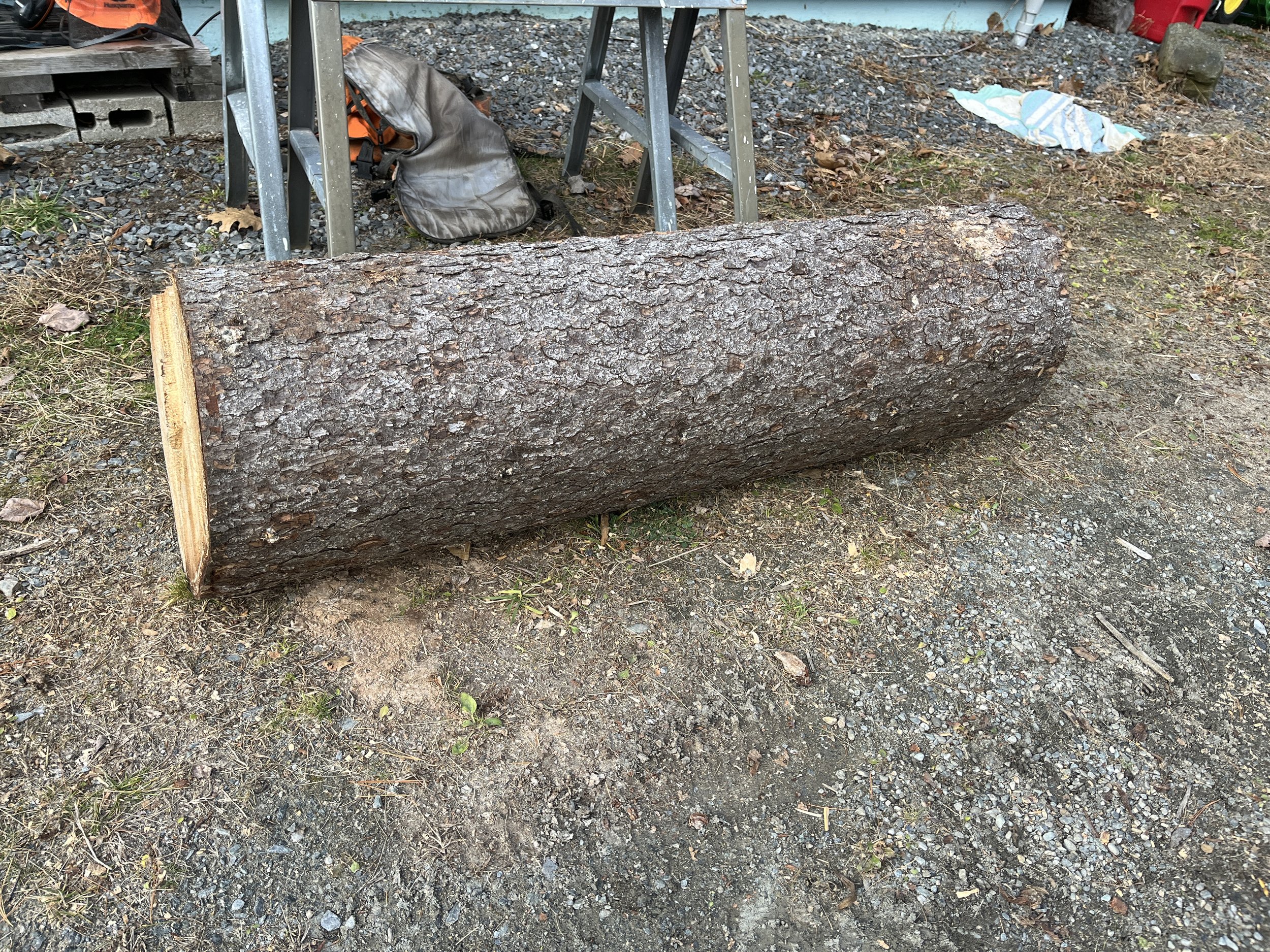
Local white spruce salvaged from the Dartmouth Skiway.
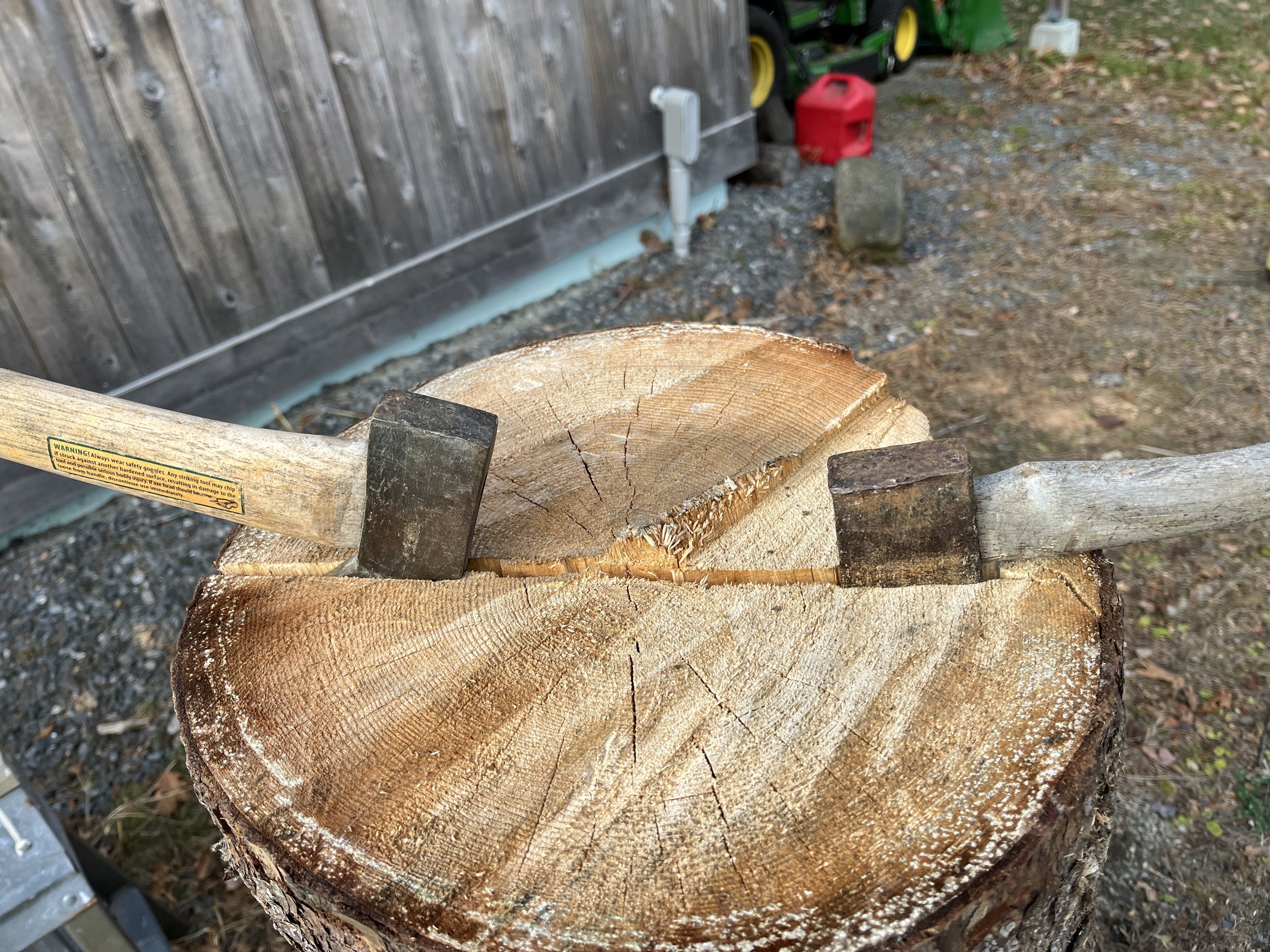
Hand split spruce yields straight billets with perfect vertical grain. This makes the soundboard lighter, stiffer, and more responsive.
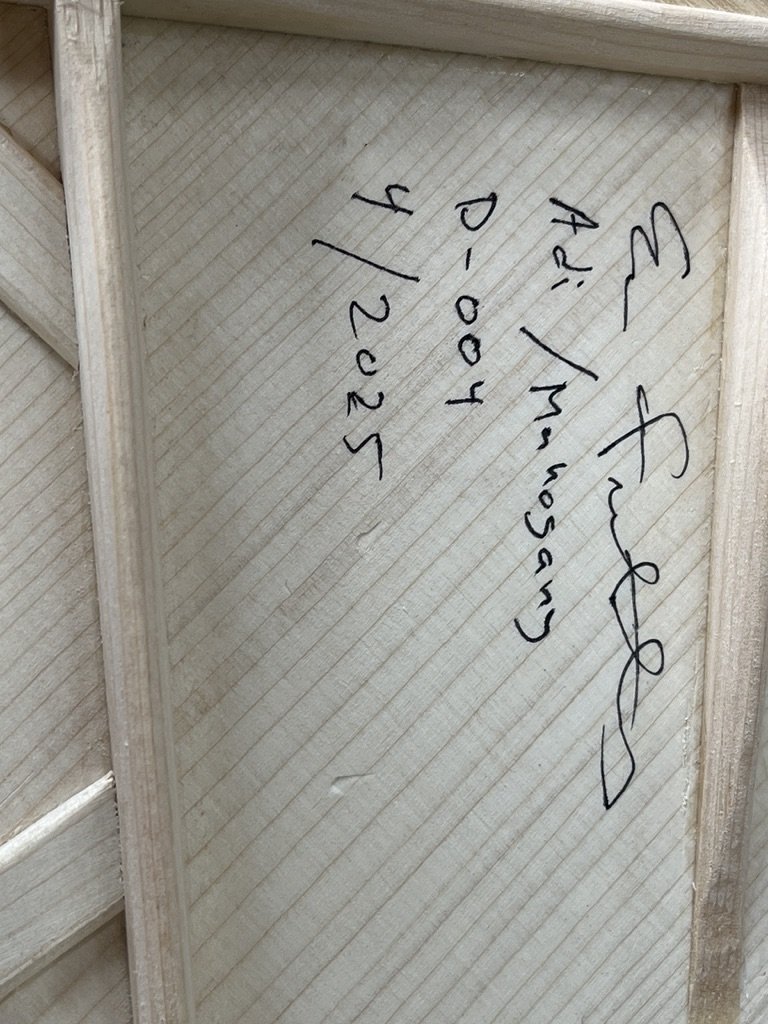
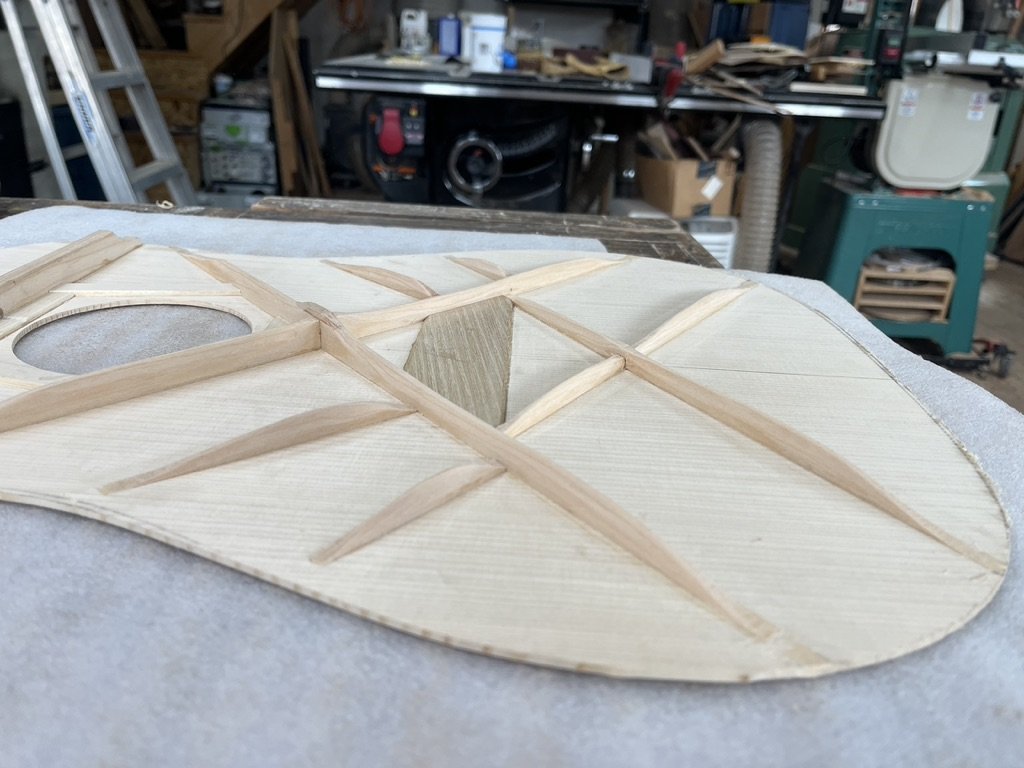
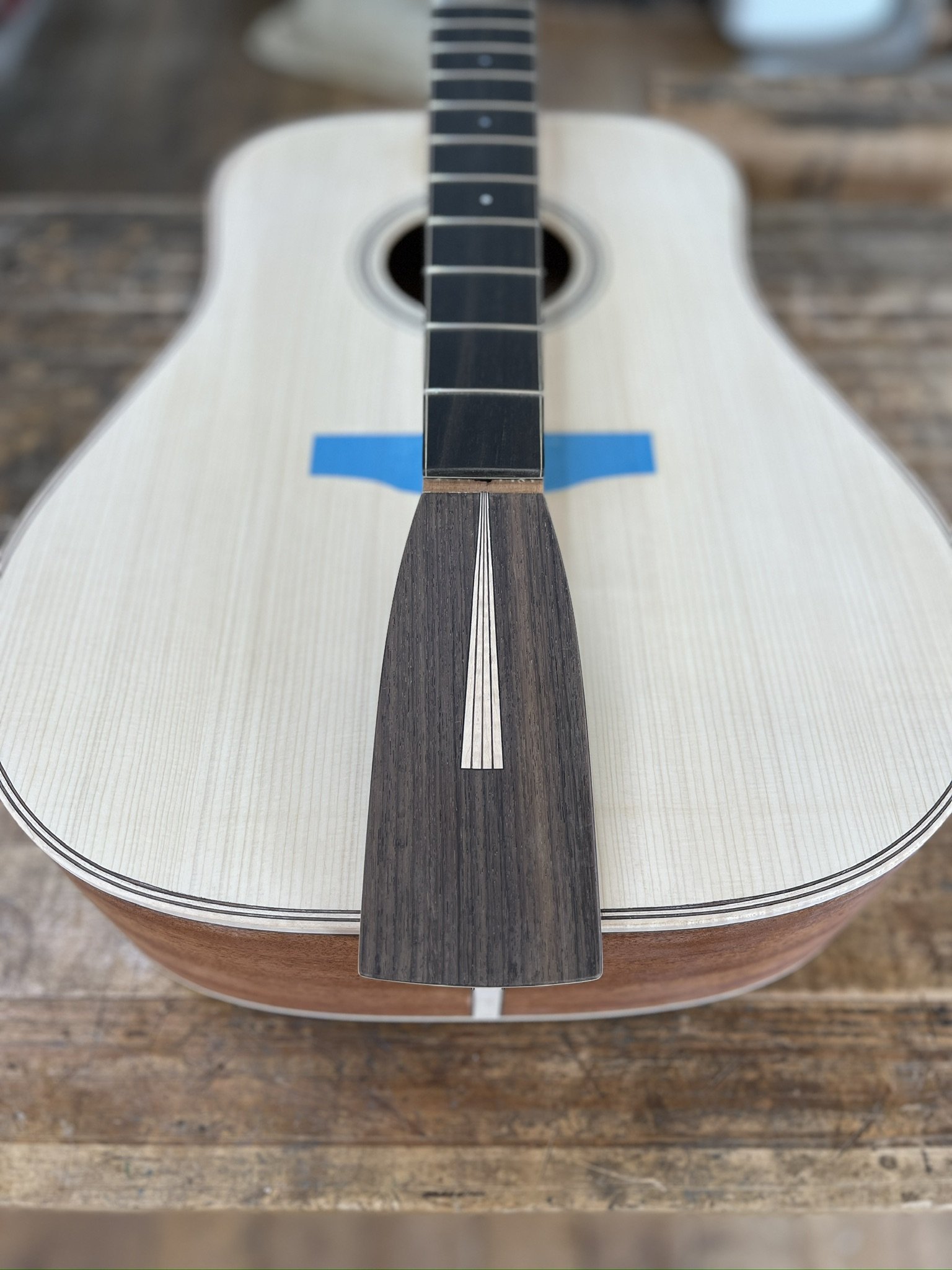
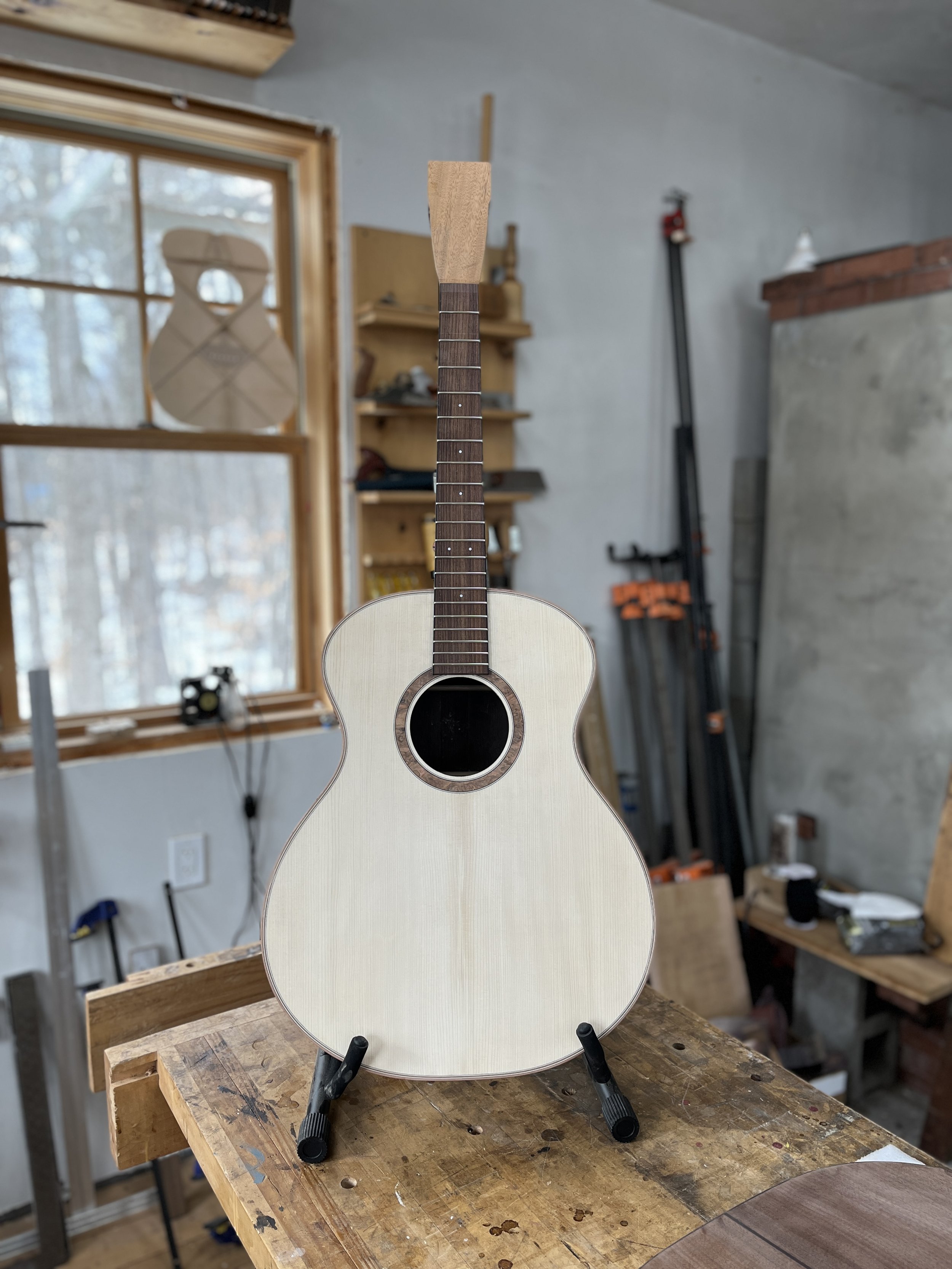
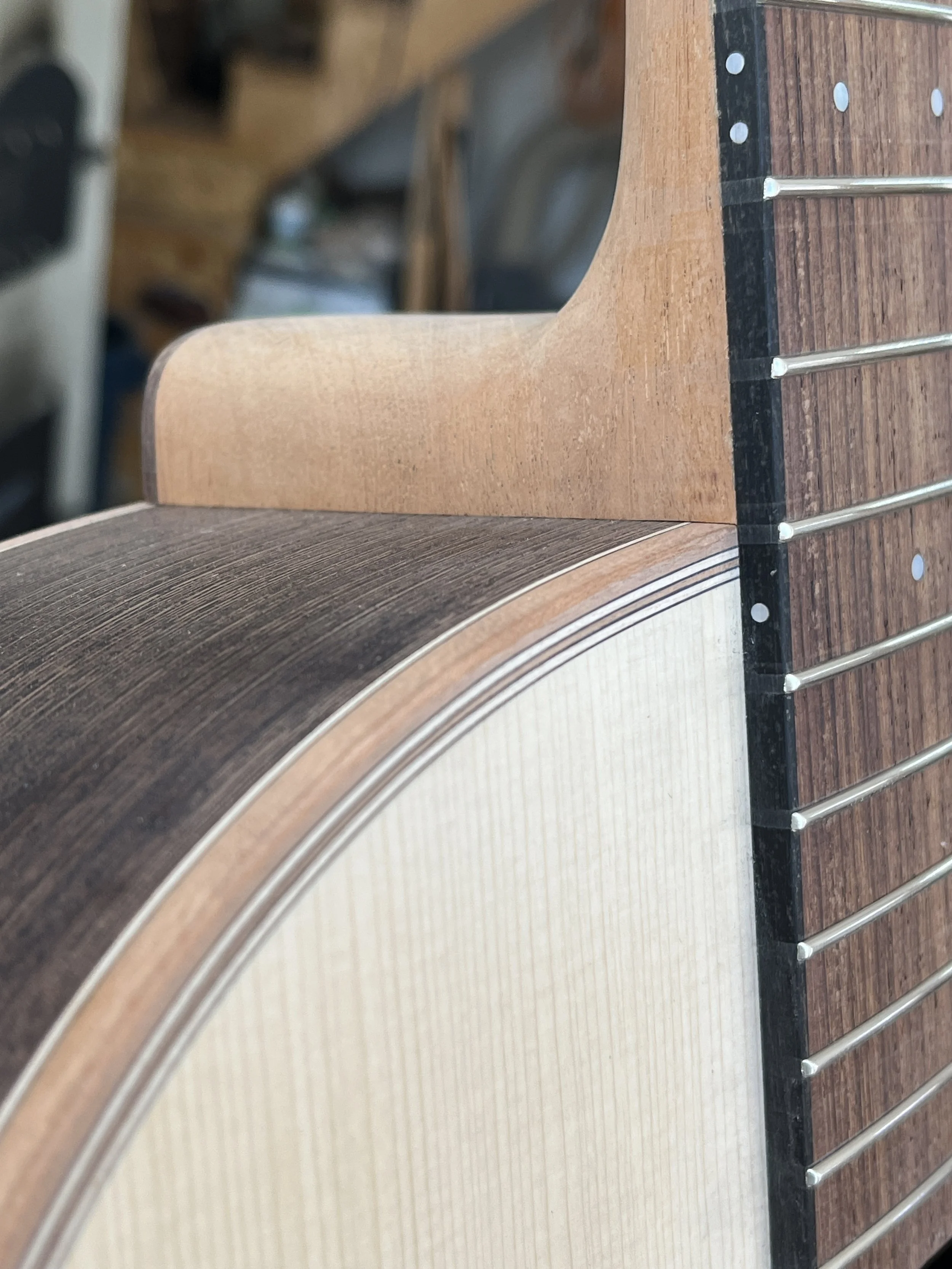

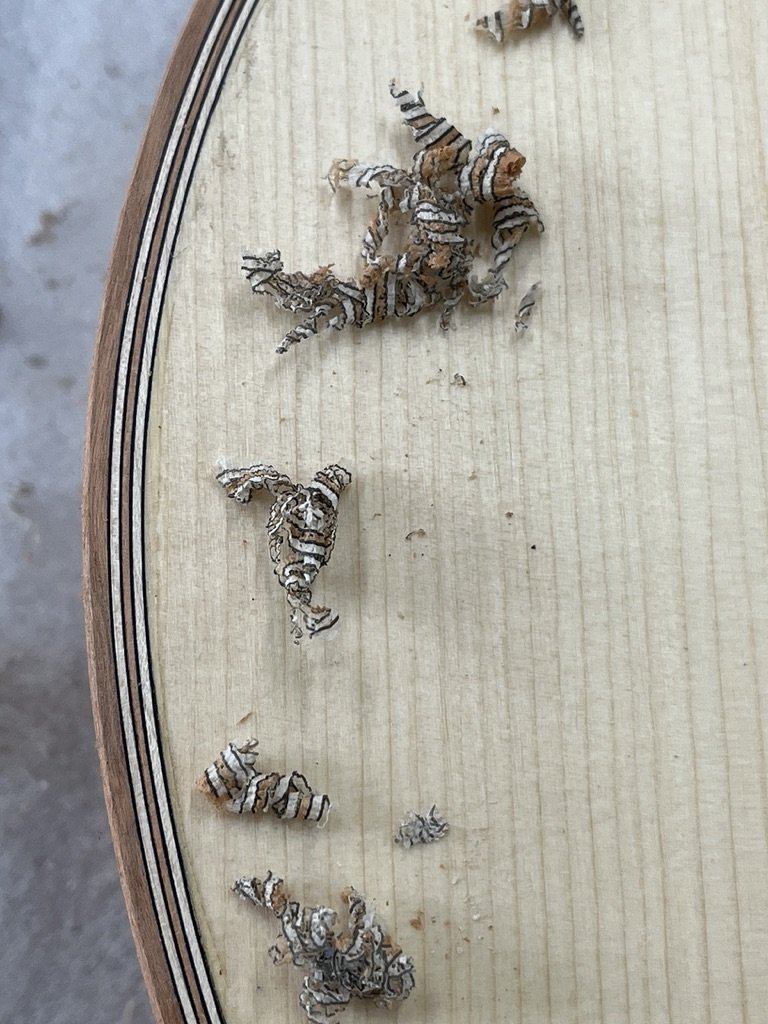
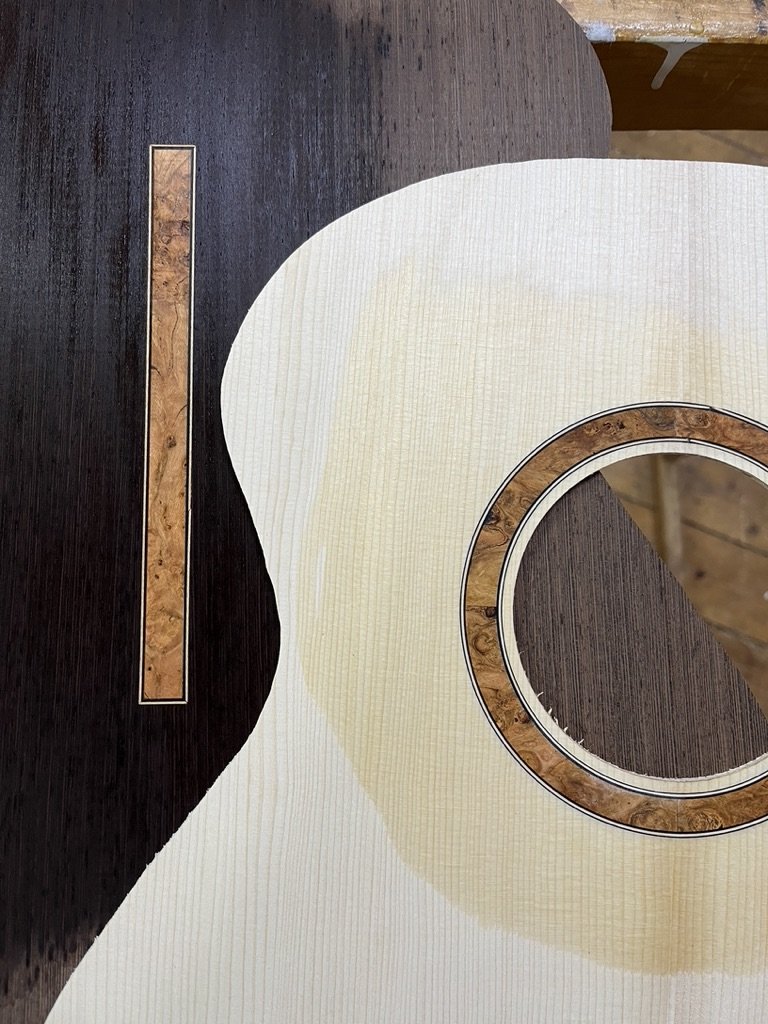
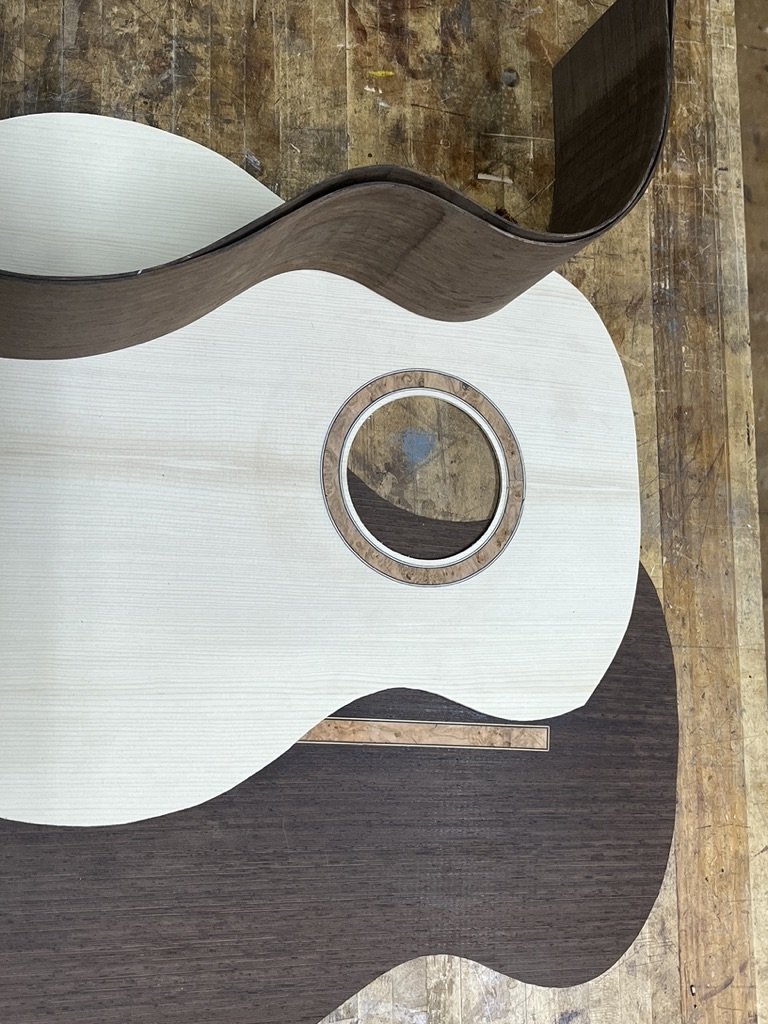
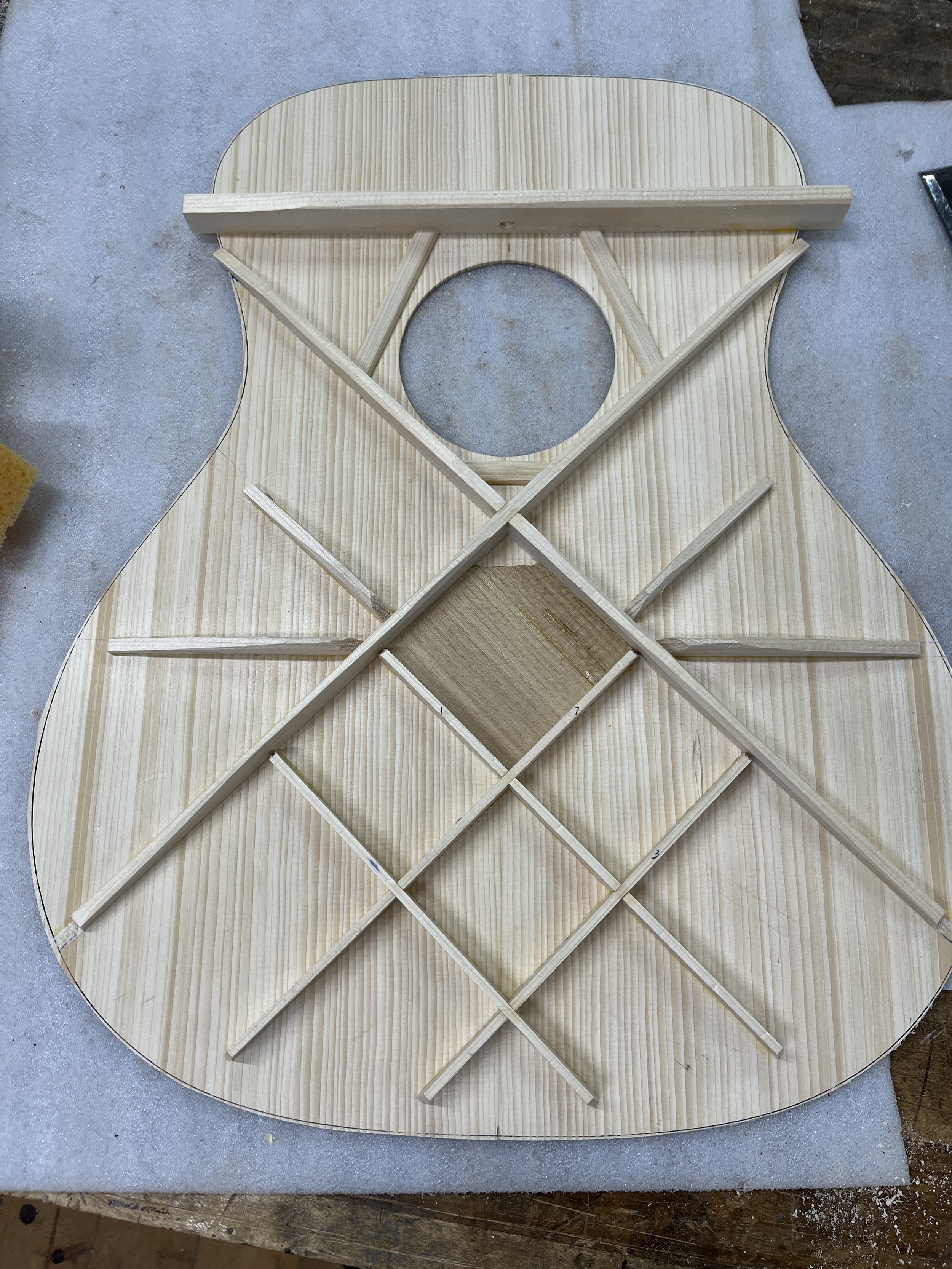
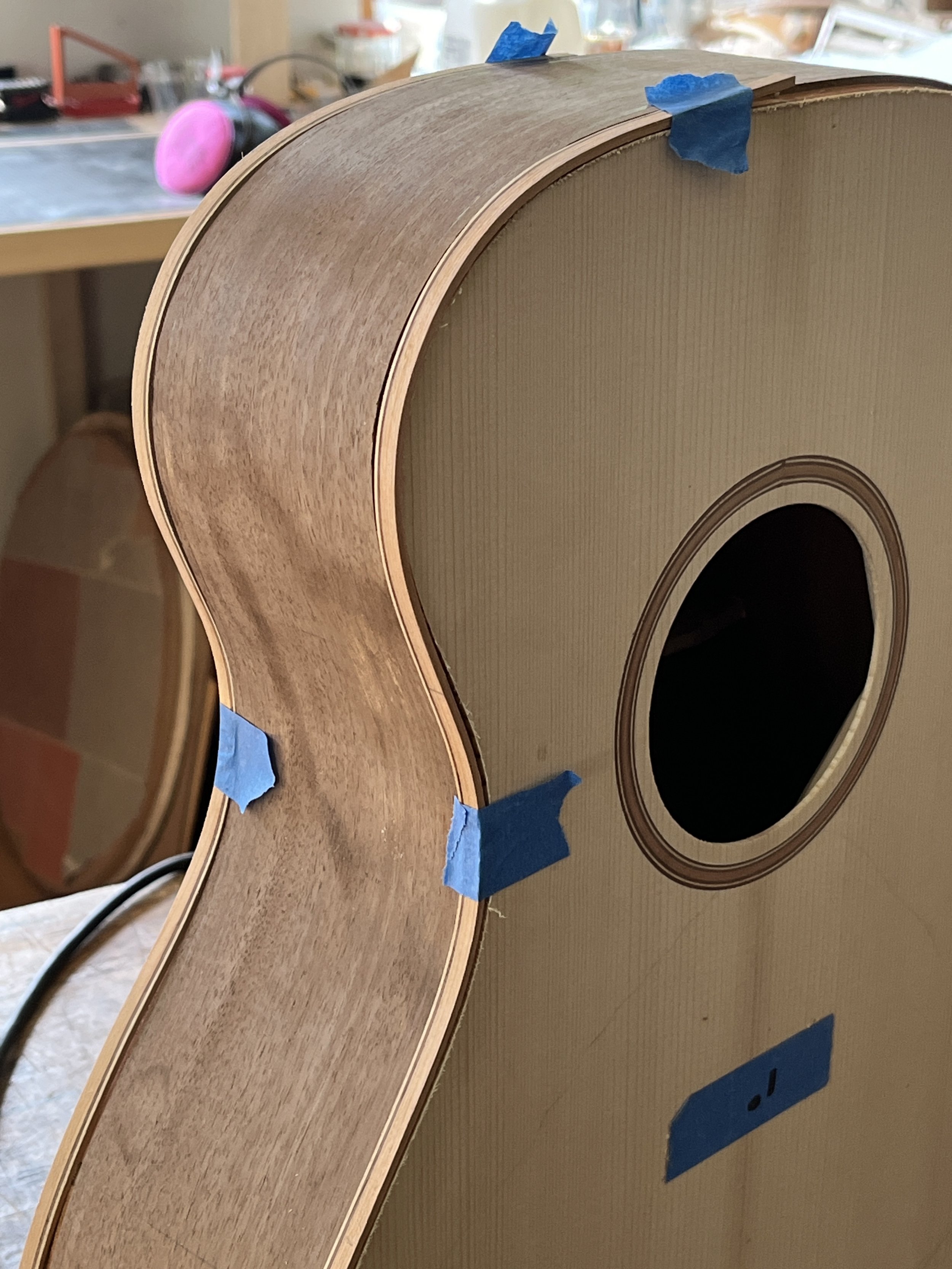
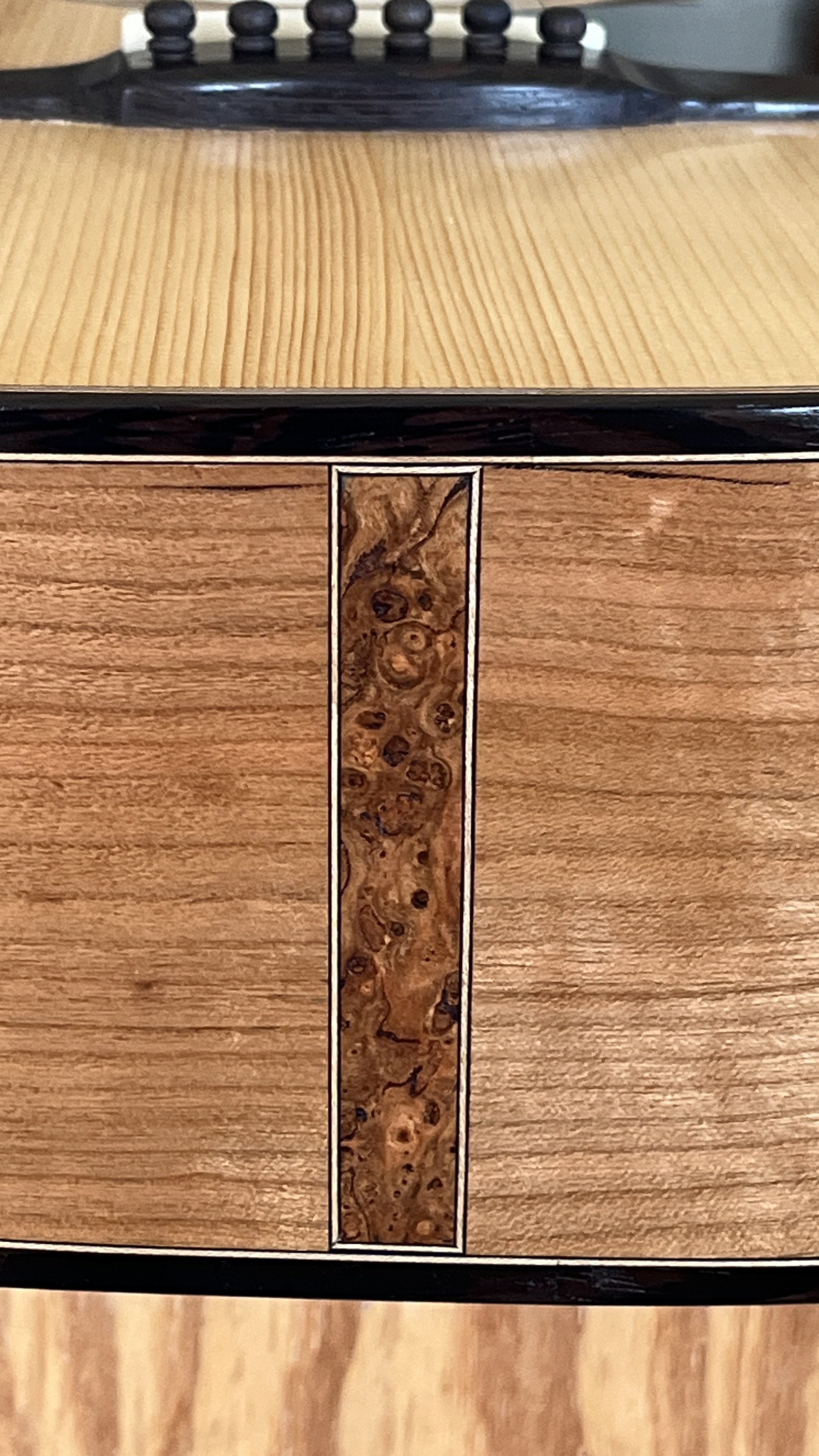
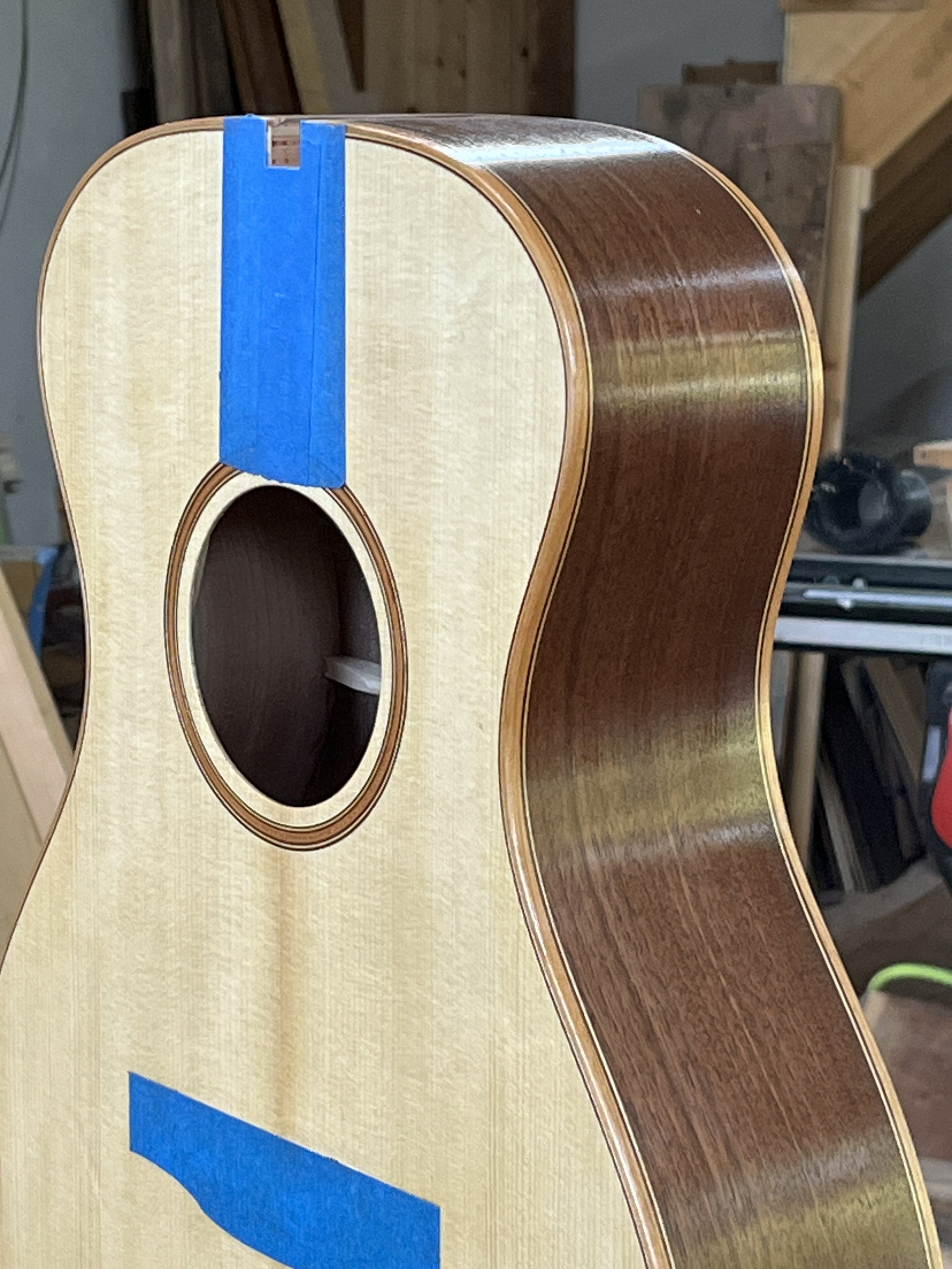
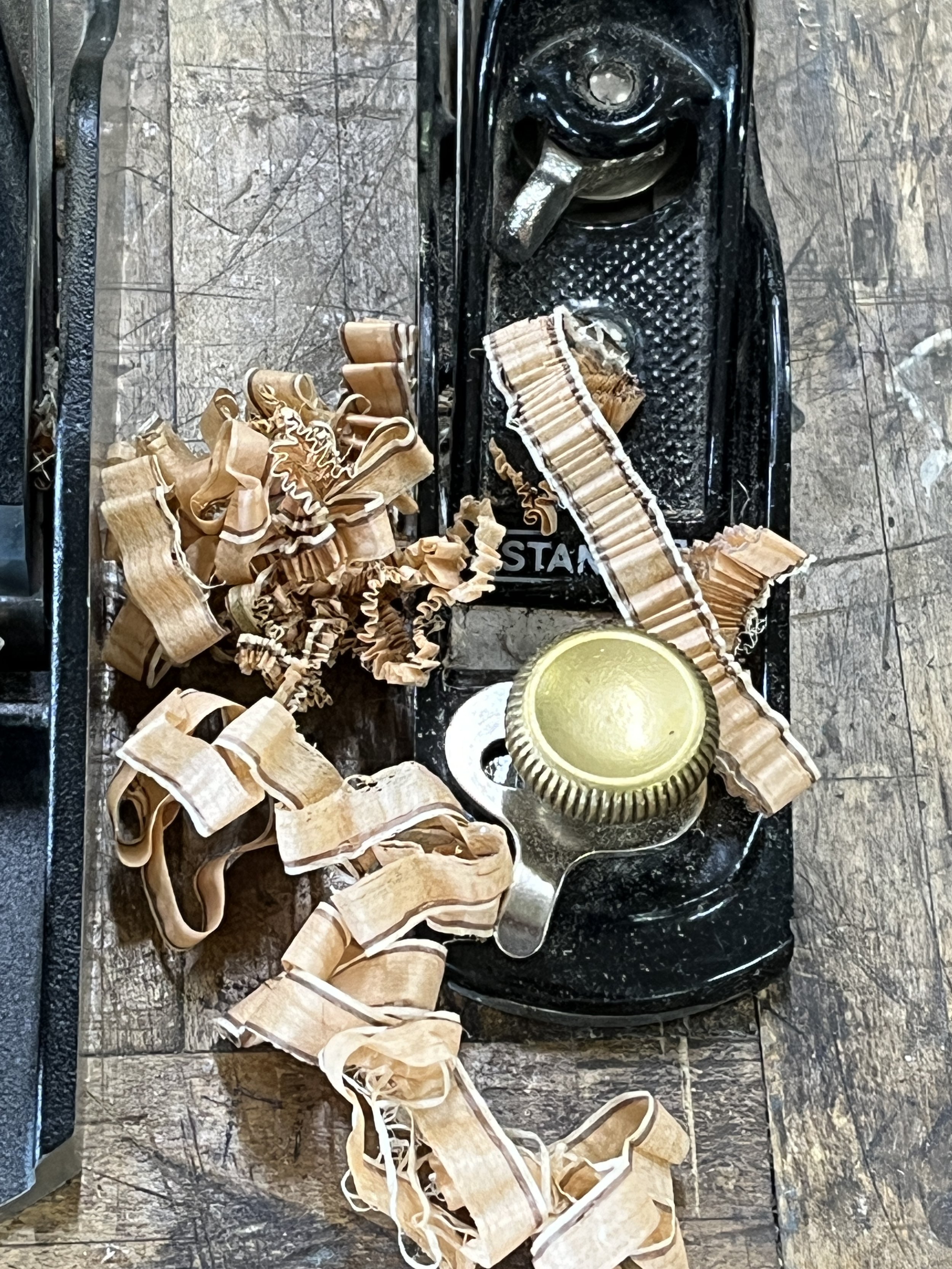
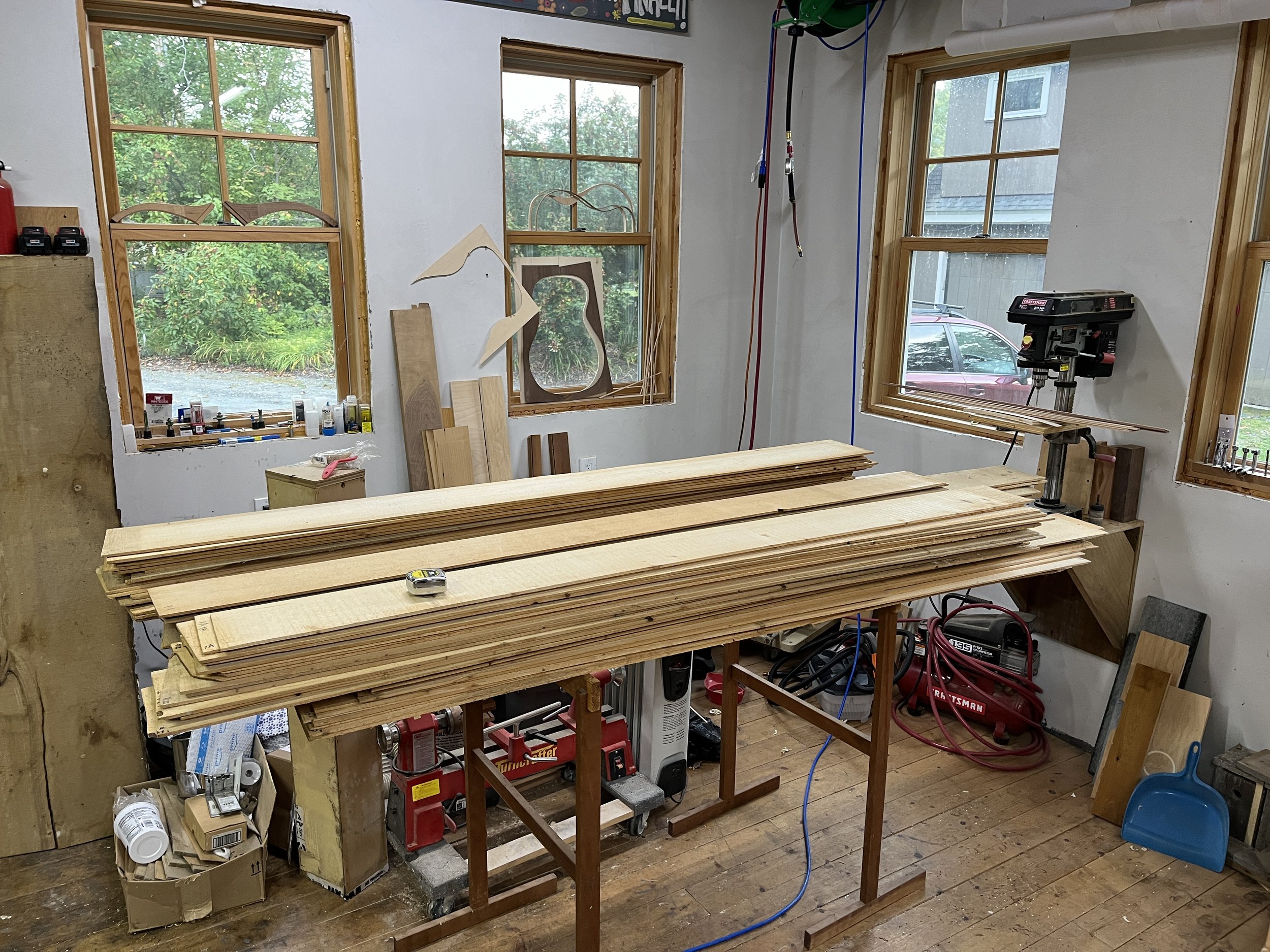
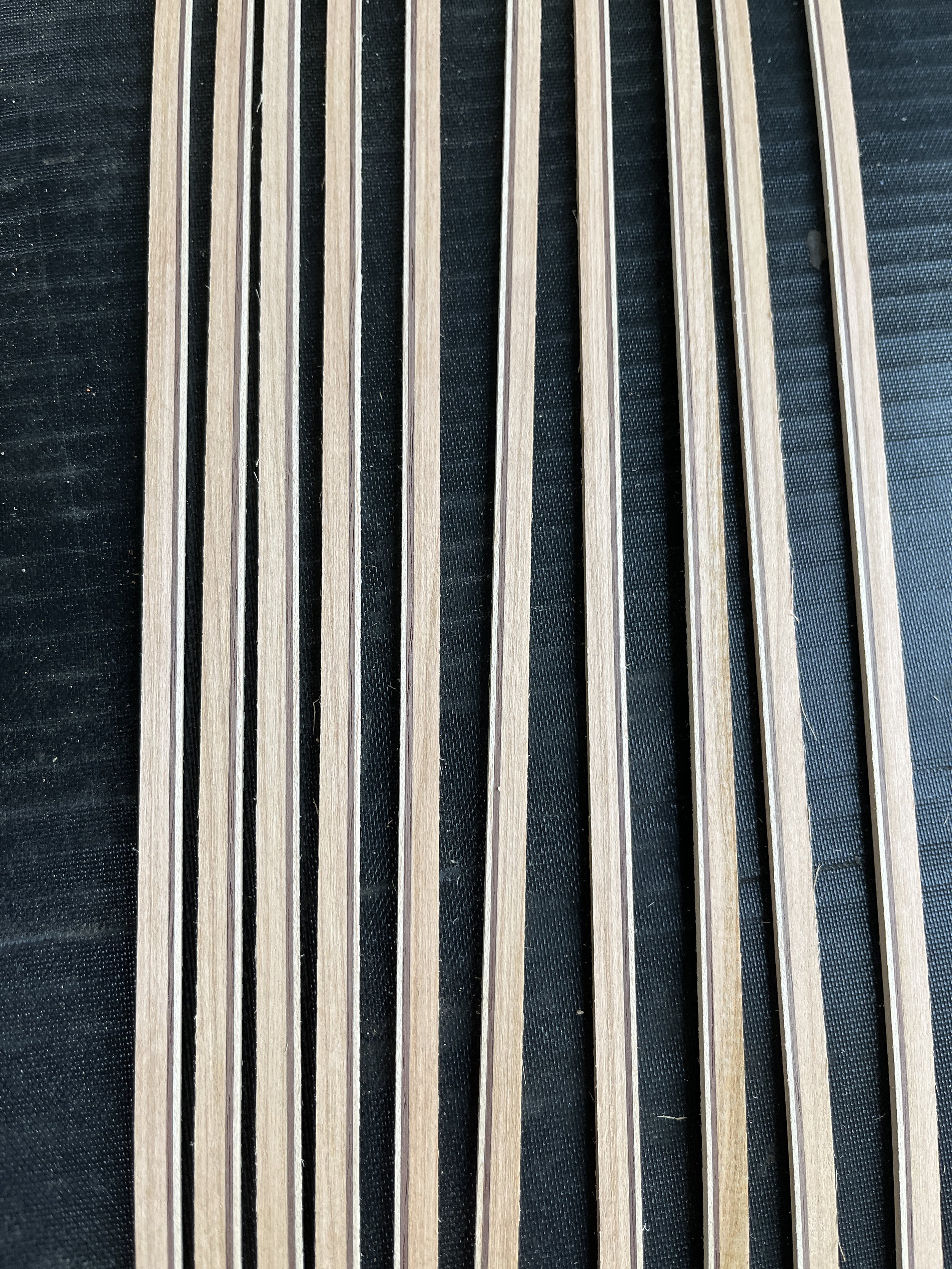

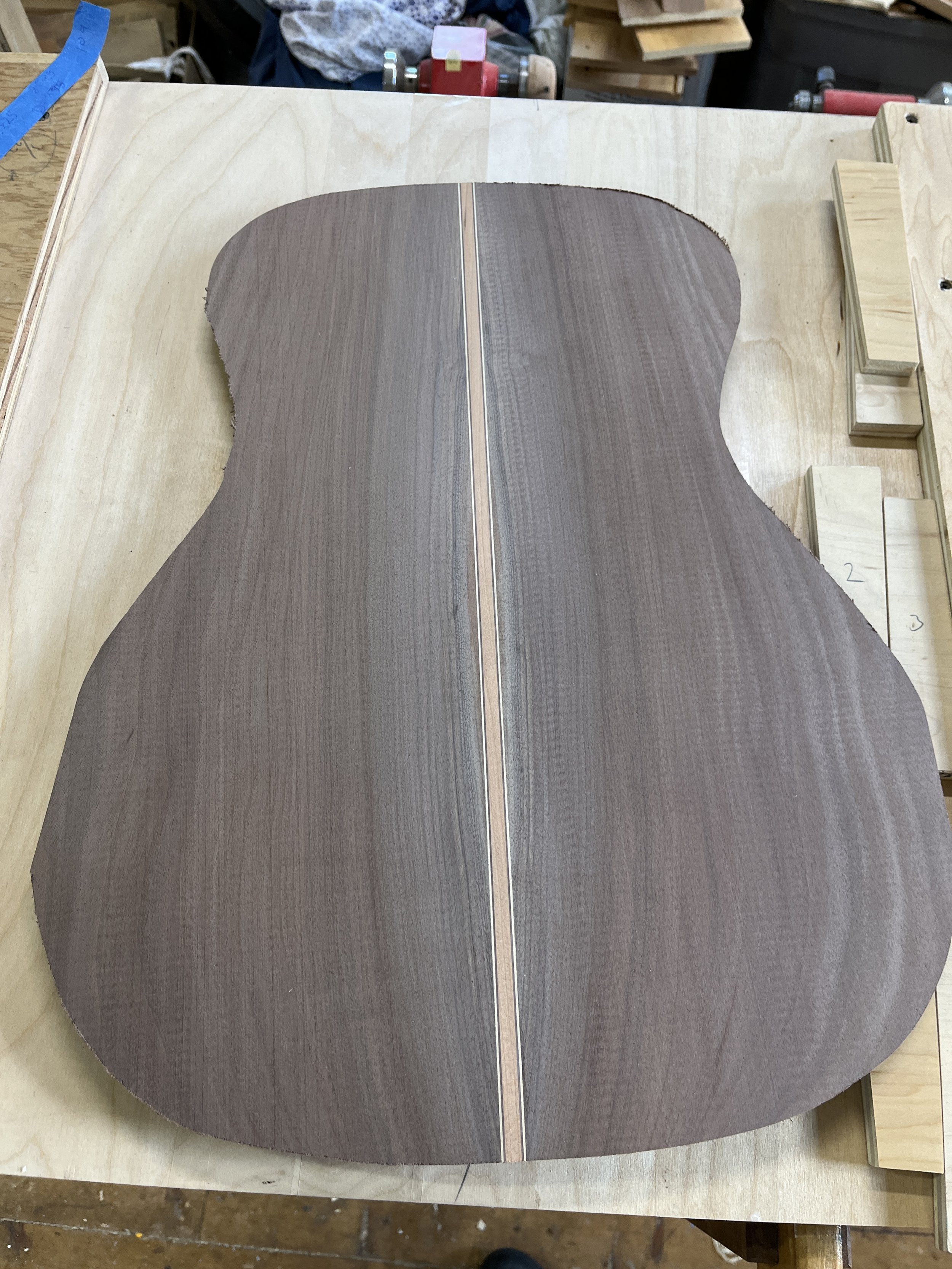
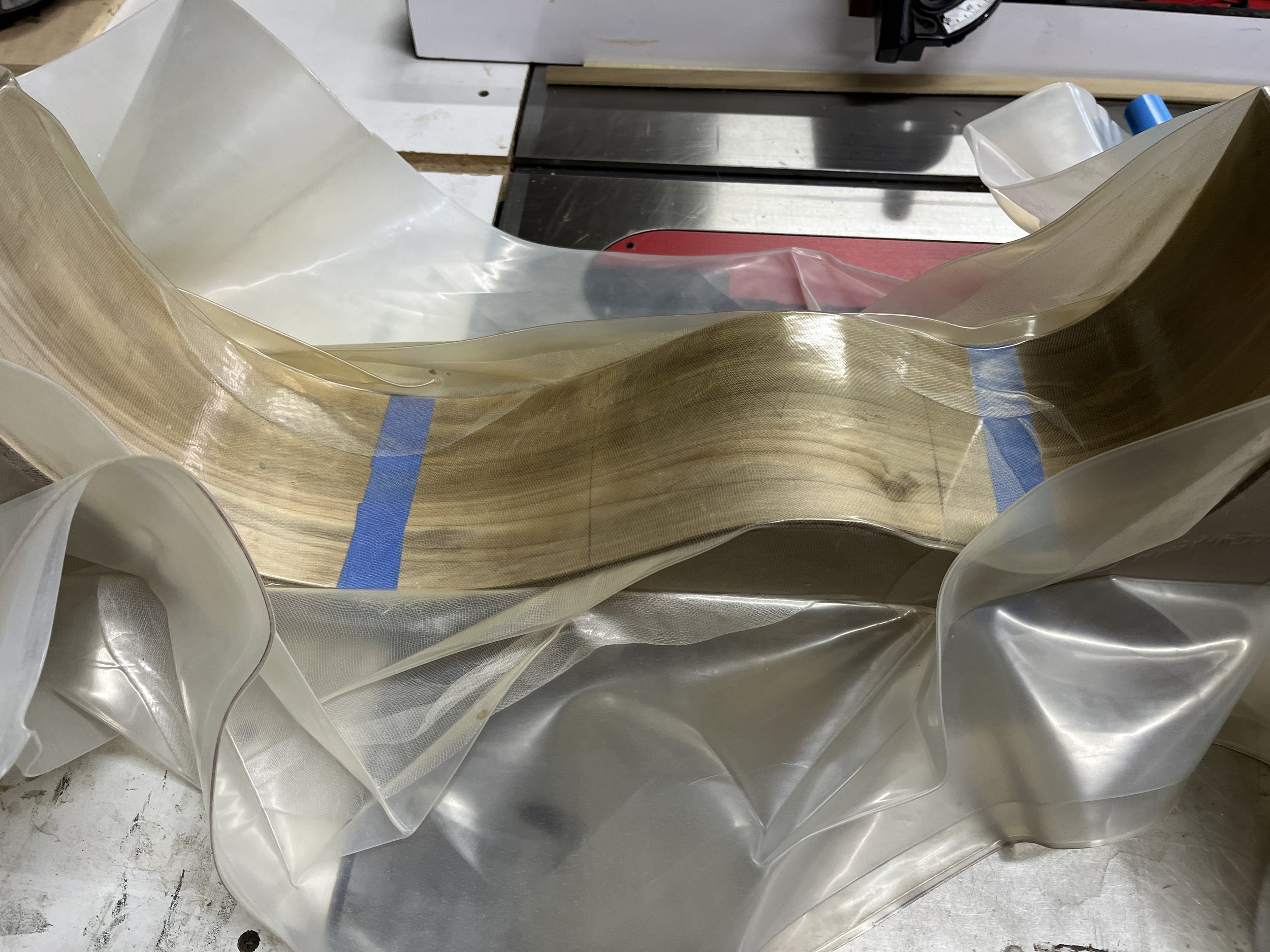



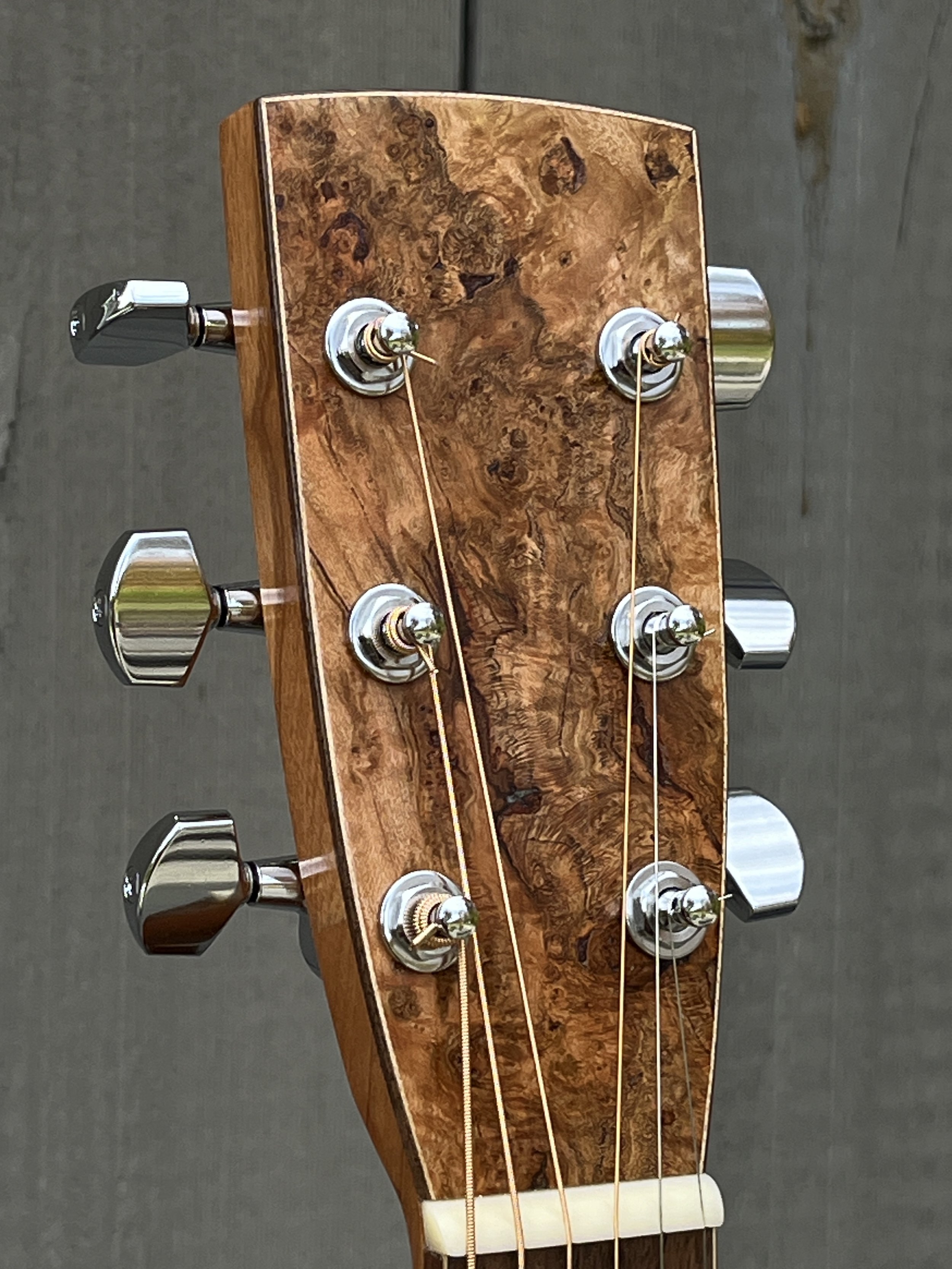
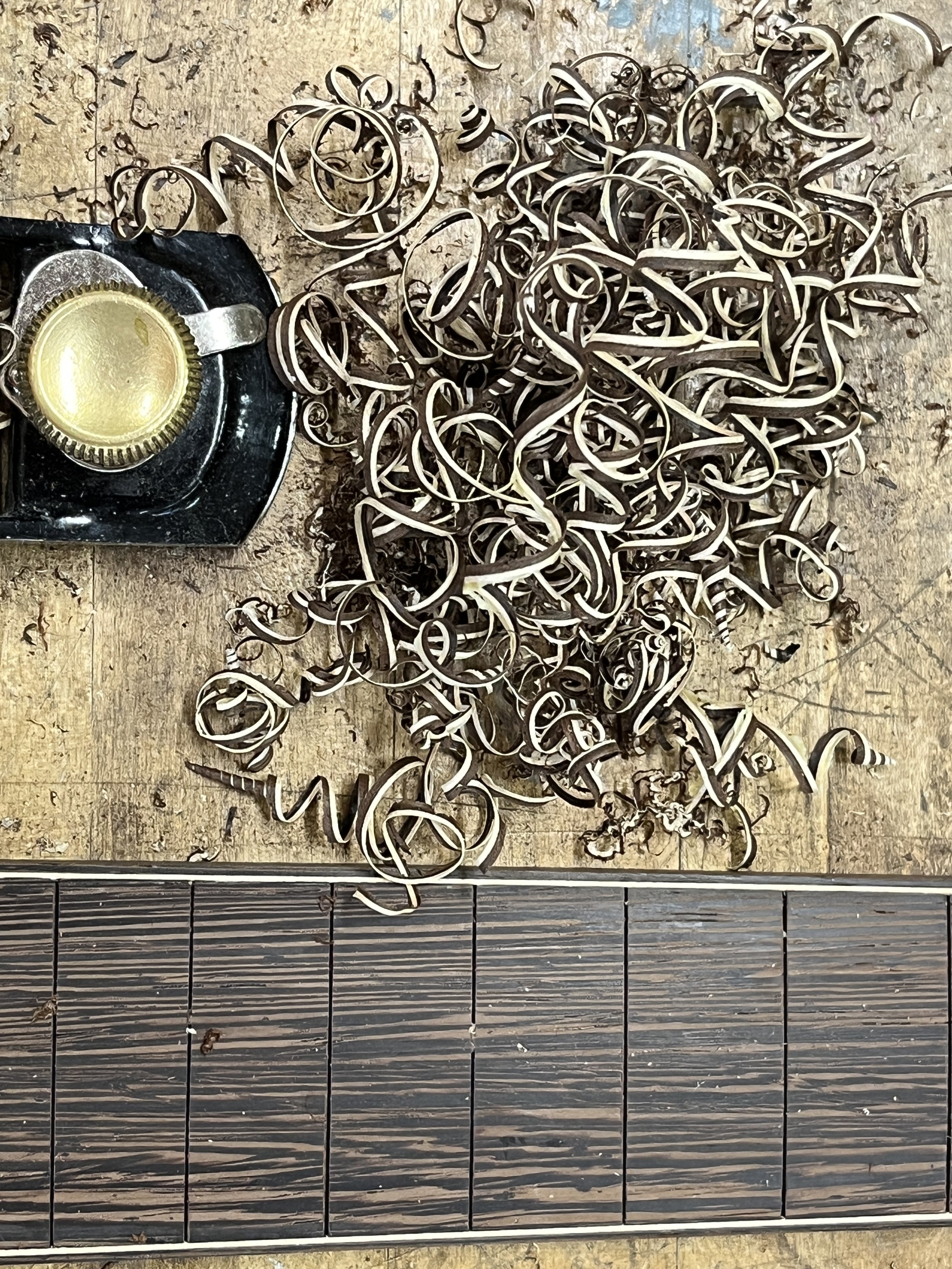
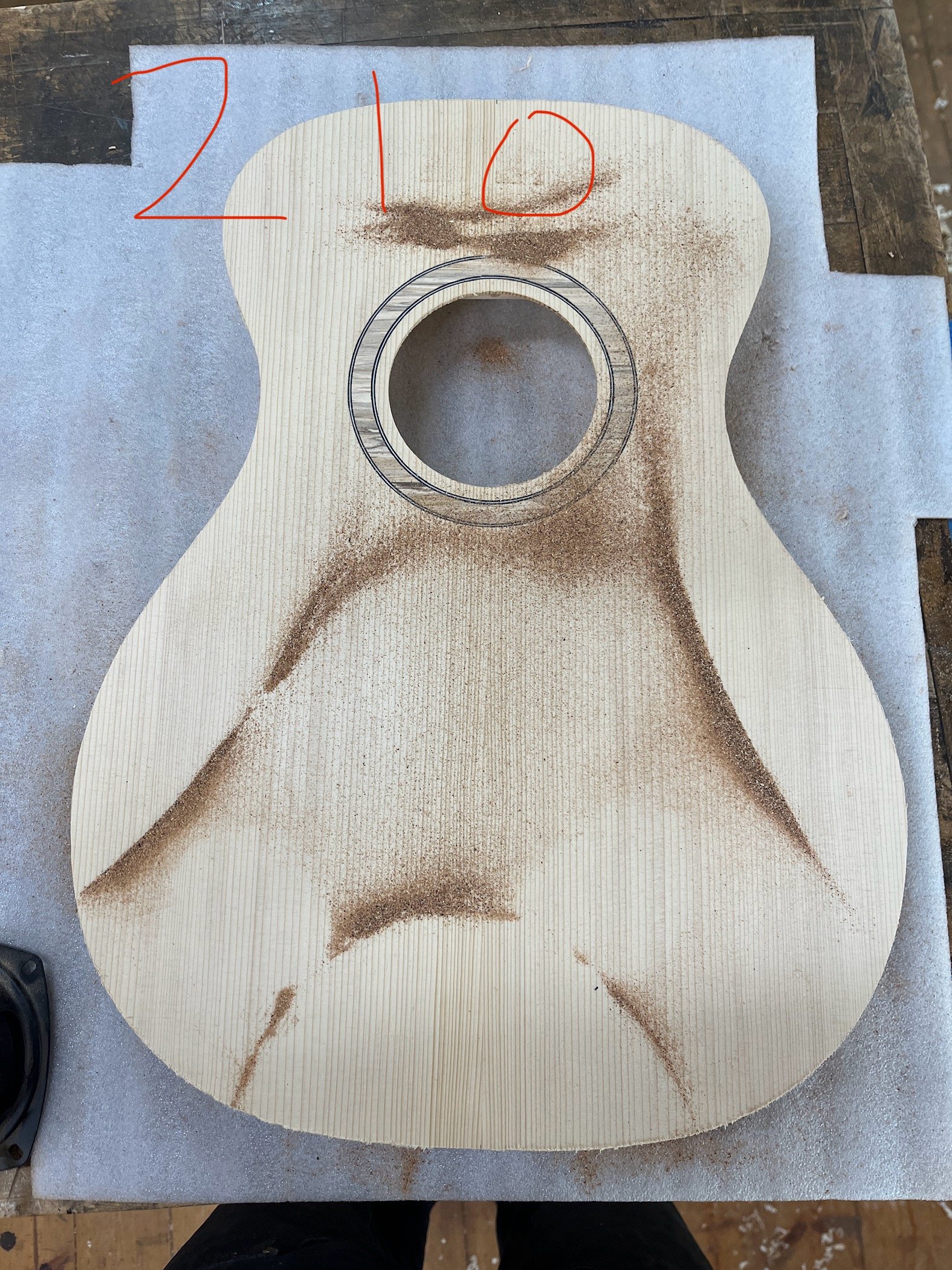
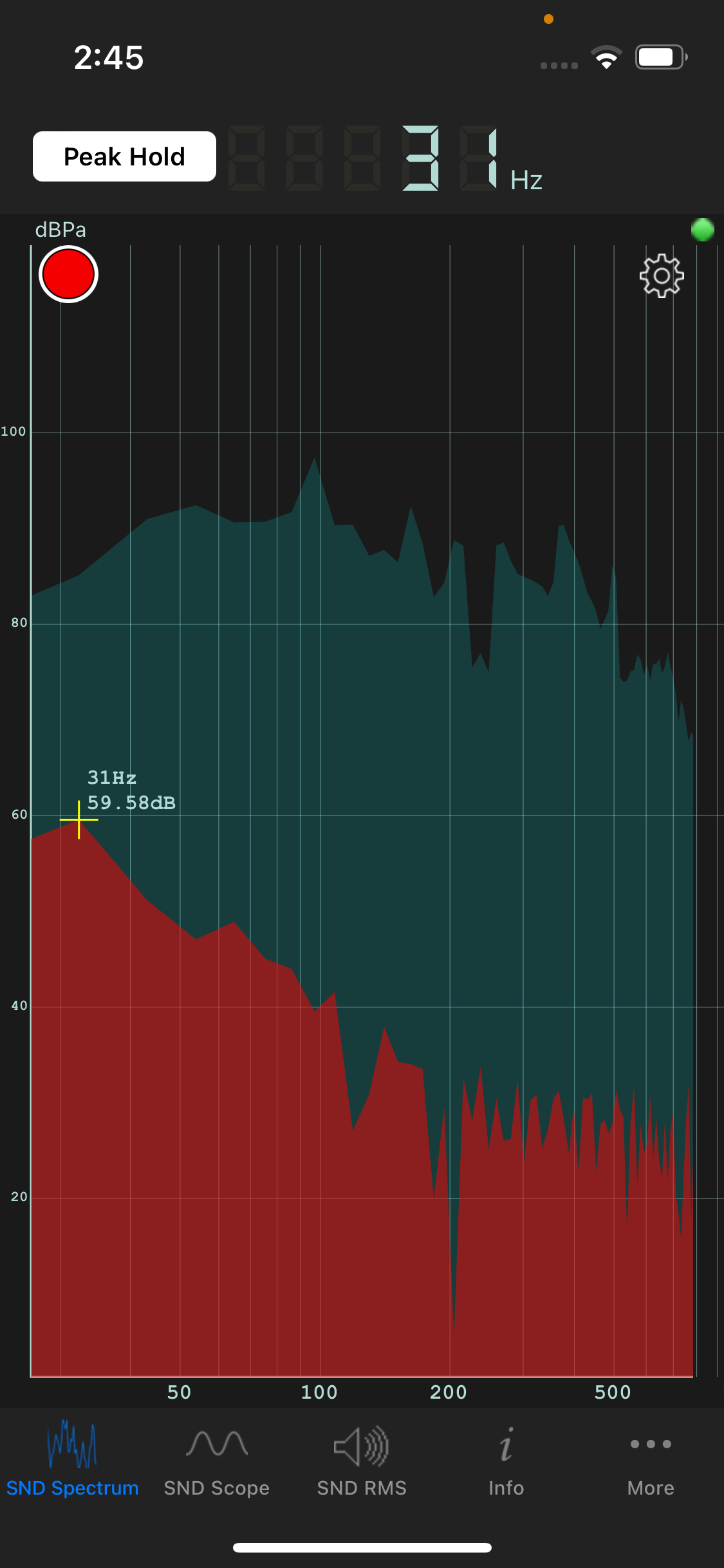

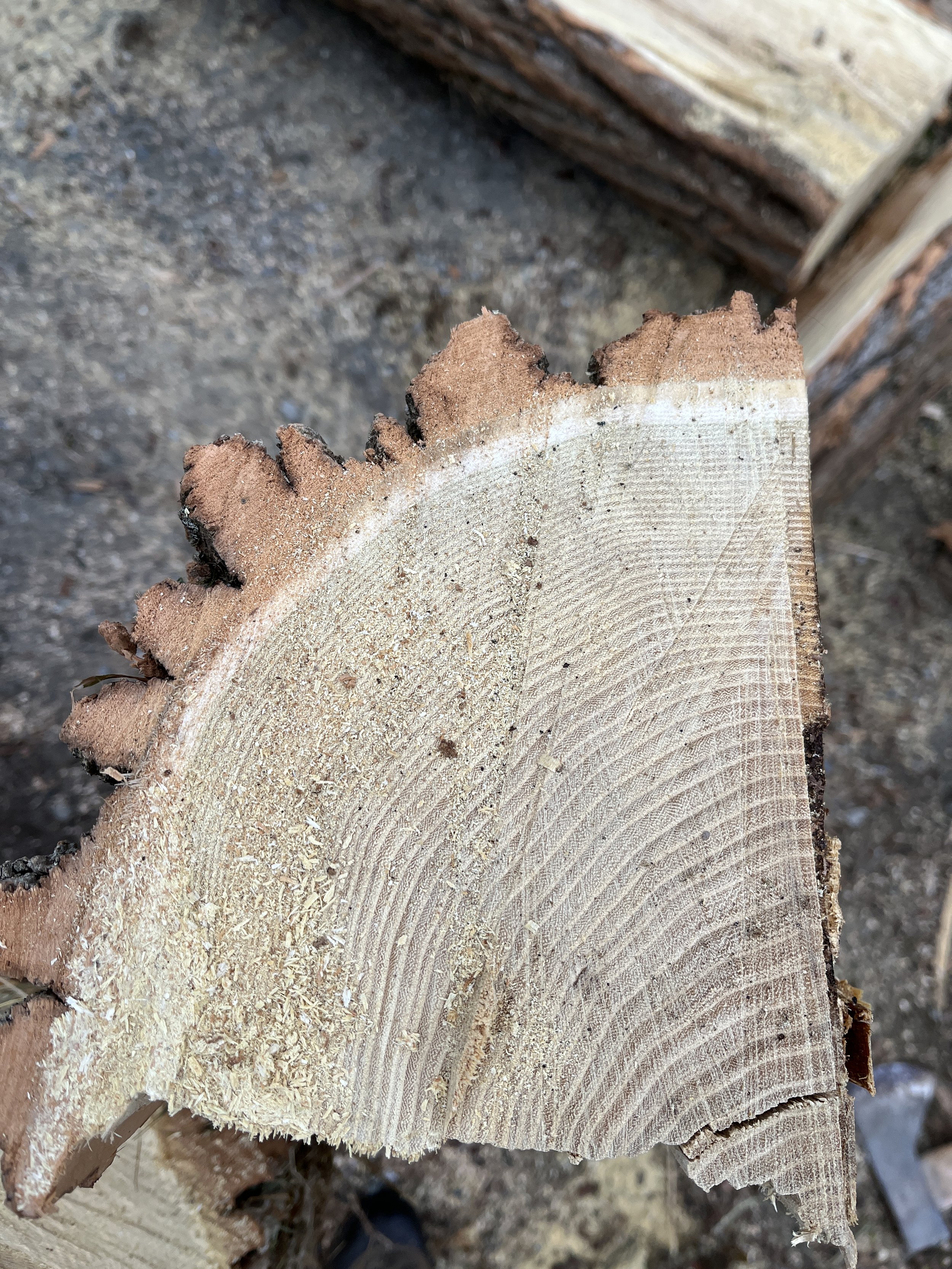
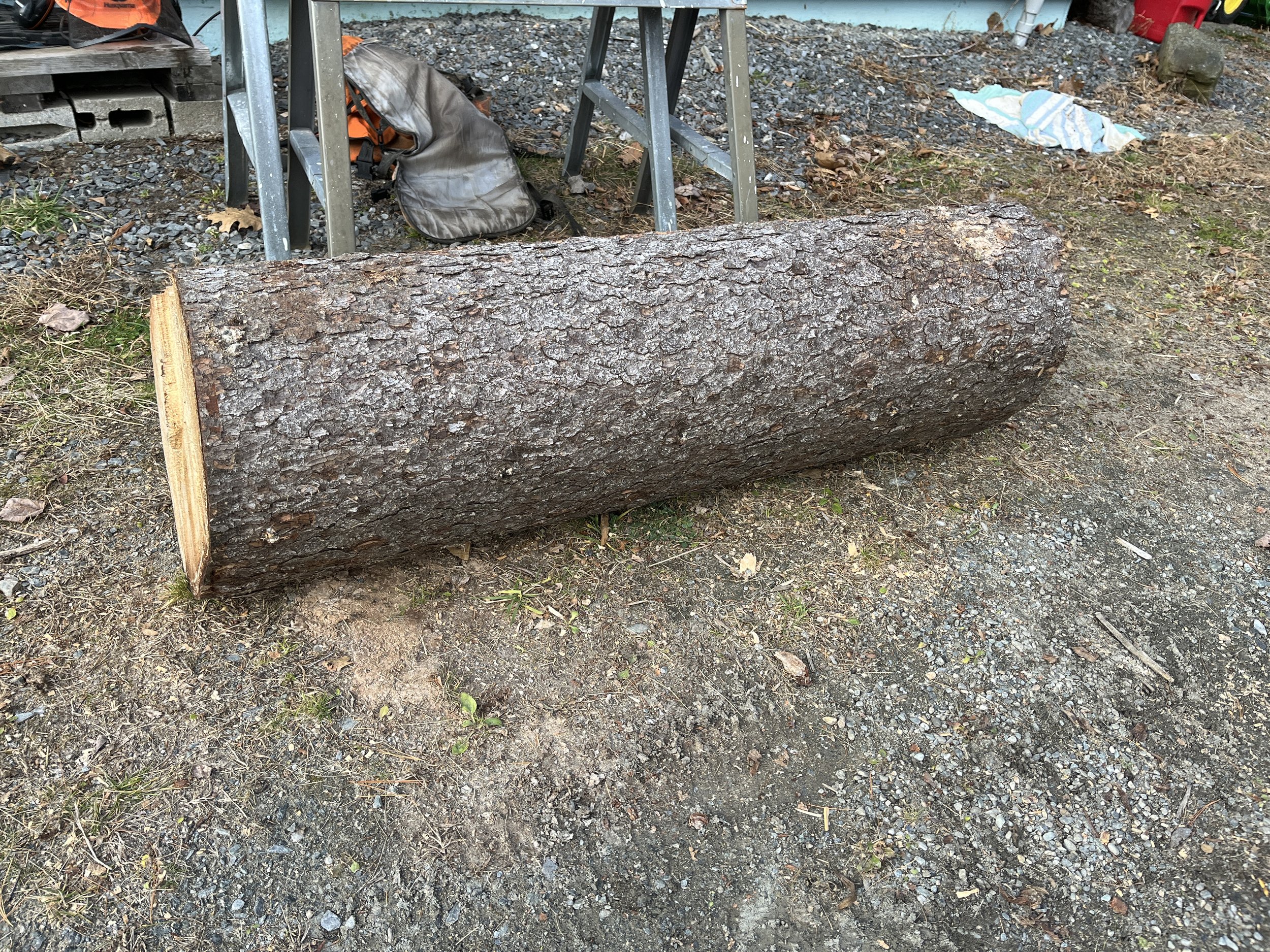
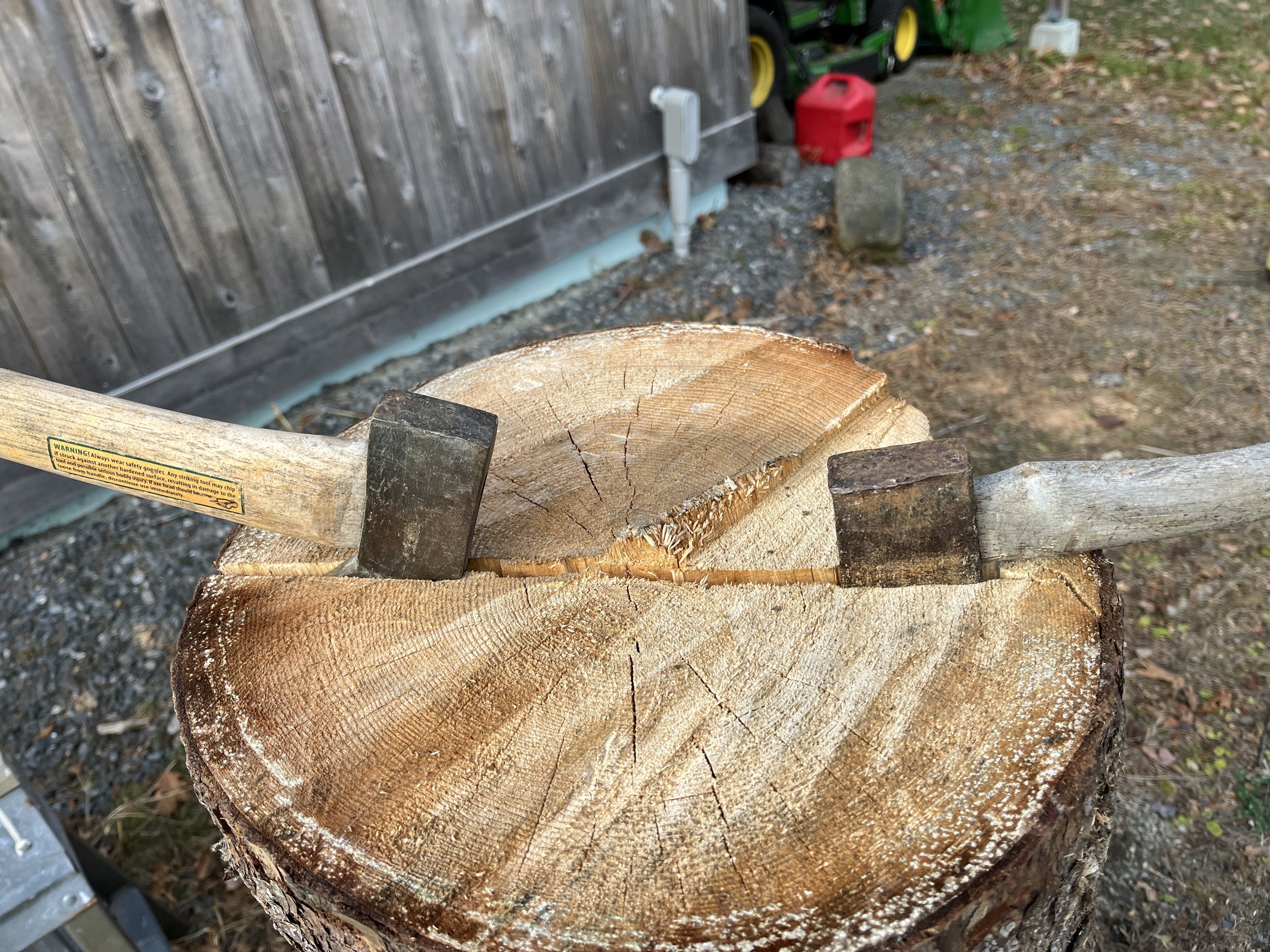
This is not my guitar, but I made it!
I’ve been working on hybrid scalloped/tapered bracing, to provide fast attack and lots of overtones.
Red spruce, rosewood fingerboard with ebony binding.
Cherry binding with black/maple/jatoba purfling.
Wenge back and sides, mahogany neck
I love the striped shavings from a handplane
Detail of Cherry burl rosette and back inlay
Beginnings of a Small Jumbo for fingerstyle players.
Never stop learning. This is a X-lattice hybrid bracing developed by Ervin Somogyi and used by many modern builders. It gives the builder much more control over voicing the instrument.
Almost there…these need to fit perfectly. It is a time consuming process.
End graft using local cherry burl
I love finishing guitars…after all the time and effort, it is so great to see them with finish.
Nothing beats a handplane for fine work.
A load of red spruce ready for processing/grading. Grown in Lyme NH. I am so lucky to be able to work with this excellent material!
Binding and side purfling ready for bending and fitting. I see a few extras…there is always some breakage.
Modern headstock/neck volute. Provides extra support for the headstock/neck and a nice backstop for your hand.
Local walnut back after trimming.
Side laminations resting in the vacuum bag before gluing.
Amazing!
Local spalted elm soundhole rosette and wenge and maple binding/purfling.
Harvested locally
Harvested locally
Trimming fingerboard binding. Sneak up on the perfect fit.
Using Chladni patterns to tune a soundboard. This involves driving a top at different frequencies to identify different modes of vibration
Using the frequency spectrum to tune a top.
Local black locust logs awaiting processing into billets for backs and sides. Black locust is an excellent alternative to imported rosewood.
Black locust split and quartered by hand. This yields straight billets with perfect vertical grain. For the guitar this means stronger and more resonant backs and sides.
Local white spruce salvaged from the Dartmouth Skiway.
Hand split spruce yields straight billets with perfect vertical grain. This makes the soundboard lighter, stiffer, and more responsive.